how to clean sintered glass filter | Lvyuan Guide
Maintaining the efficiency of sintered glass filters is crucial for various applications. This guide offers practical cleaning methods, addressing common challenges faced by professionals. We cover effective cleaning techniques depending on the type of contamination and provide insights into preventing future blockages, ensuring optimal filter performance and longevity. Learn how to choose the right cleaning method for your specific application and extend the life of your valuable filters.
How to Clean Sintered Glass Filters: A Guide for Professionals | Lvyuan
This article addresses the common challenges professionals face in cleaning sintered glass filters, providing effective methods for maintaining optimal filter performance and extending their lifespan. Improper cleaning can damage the filter media, leading to reduced efficiency and costly replacements.
Understanding Sintered Glass Filters
* Material: Sintered glass filters are made from precisely controlled particles of borosilicate glass, fused together to create a porous structure. This structure provides excellent chemical resistance and temperature stability.
* Porosity: Porosity varies depending on the manufacturing process, influencing the filter's ability to remove specific particle sizes. Understanding the porosity rating of your filter is vital for selecting appropriate cleaning methods.
* Applications: Widely used in diverse fields, including chemical processing, pharmaceuticals, and water purification, requiring effective cleaning protocols to ensure consistent performance.
Choosing the Right Cleaning Method
The optimal cleaning method for your sintered glass filter depends heavily on the type and extent of contamination.
* Water-Based Cleaning: For removal of easily soluble contaminants, rinsing with deionized or distilled water is often sufficient. Ultrasonic cleaning can enhance this process, removing fine particles from the pores.
* Solvent Cleaning: For more stubborn contaminants, organic solvents might be necessary. Solvent selection is crucial, ensuring compatibility with the glass and the contaminant. Always consult material safety data sheets (MSDS) before using any solvent.
* Acid/Base Cleaning: In cases of specific chemical residue, mild acid or base solutions might be required. This step necessitates careful consideration of filter material compatibility and appropriate neutralization procedures.
* Backwashing: For filters experiencing minor blockages, backwashing with a suitable liquid can effectively dislodge trapped particles.
Cleaning Procedures and Best Practices
* Pre-cleaning inspection: Assess the filter's condition before cleaning to determine the appropriate method and avoid unnecessary steps.
* Safety precautions: Always wear appropriate personal protective equipment (PPE), including gloves and eye protection, during cleaning. Work in a well-ventilated area.
* Drying: After cleaning, allow the filter to air dry completely or use a controlled drying method to prevent residue formation. Avoid rapid temperature changes.
* Storage: Store clean filters in a clean, dry environment to prevent recontamination.
Extending Filter Lifespan
* Pre-filtration: Using a pre-filter can significantly extend the lifespan of your sintered glass filter by removing larger particles before they reach the primary filter.
* Regular Inspection: Regular inspections allow for the early detection of blockages and enable timely cleaning, preventing irreversible damage.
* Proper Handling: Avoid dropping or damaging the filter to prevent structural damage or cracking, which can affect its performance.
Conclusion
Effective cleaning is paramount for maintaining the integrity and performance of your sintered glass filters. By following these guidelines and choosing the appropriate cleaning method based on the nature of contamination, you can ensure prolonged filter lifespan and optimal filtration performance. Contact Lvyuan for further assistance with your specific filter requirements.
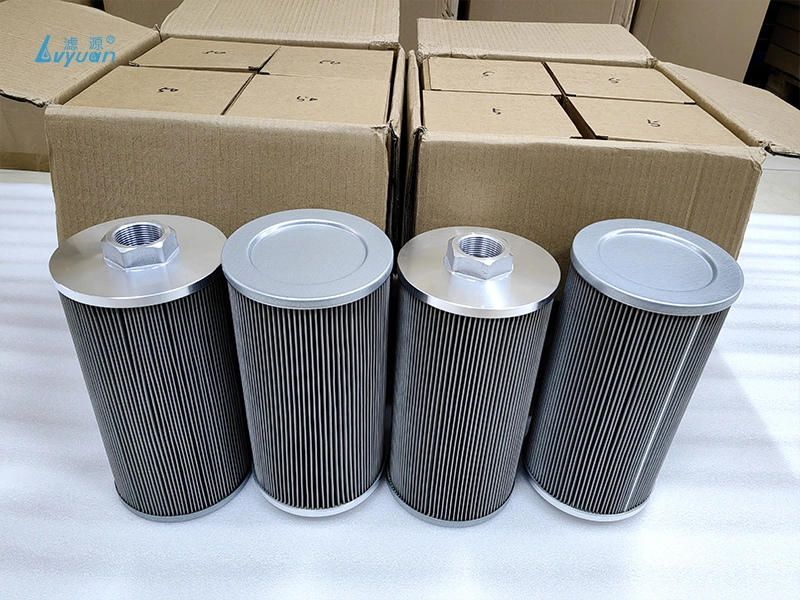
What is Sintered Metal Filter? Complete Guide by Lvyuan
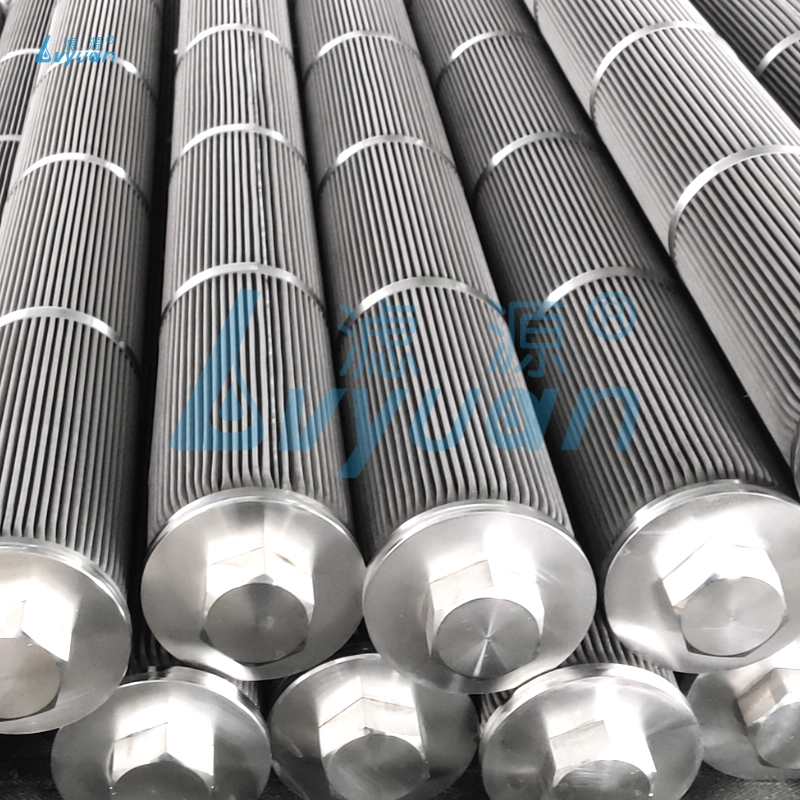
Metal Sintered Filters: Precision Filtering to Drive Industrial Upgrading
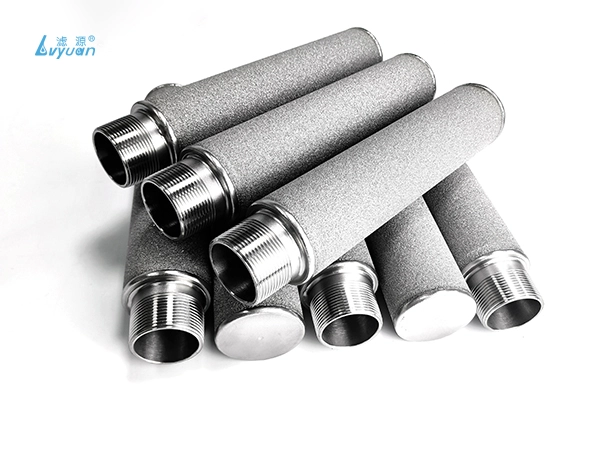
Choosing Sintered Filters: An Overview for Industrial Applications
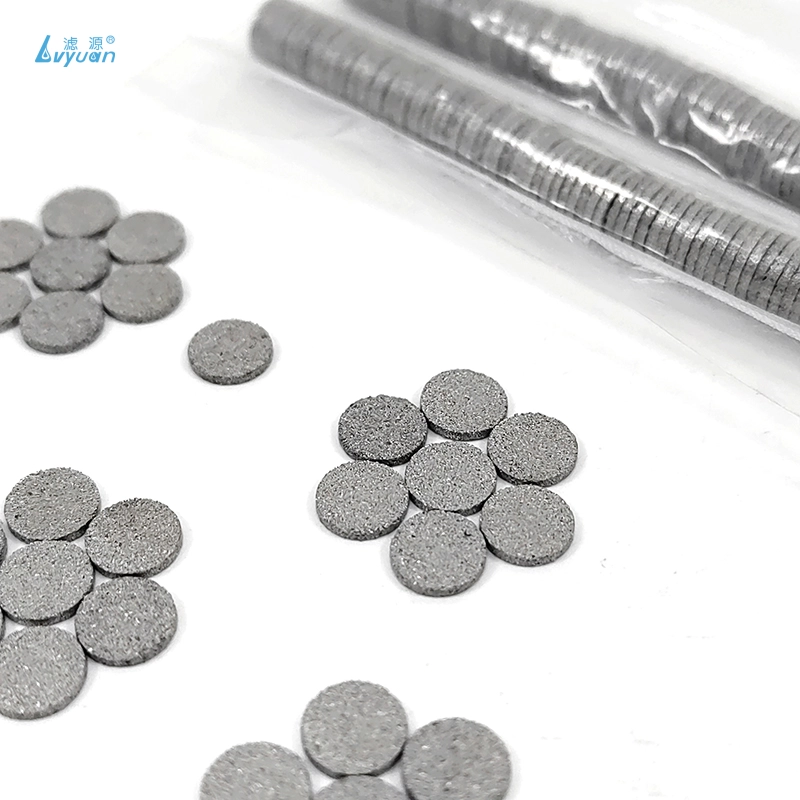
What is a Sintered Metal Filter Disc? A Comprehensive Guide
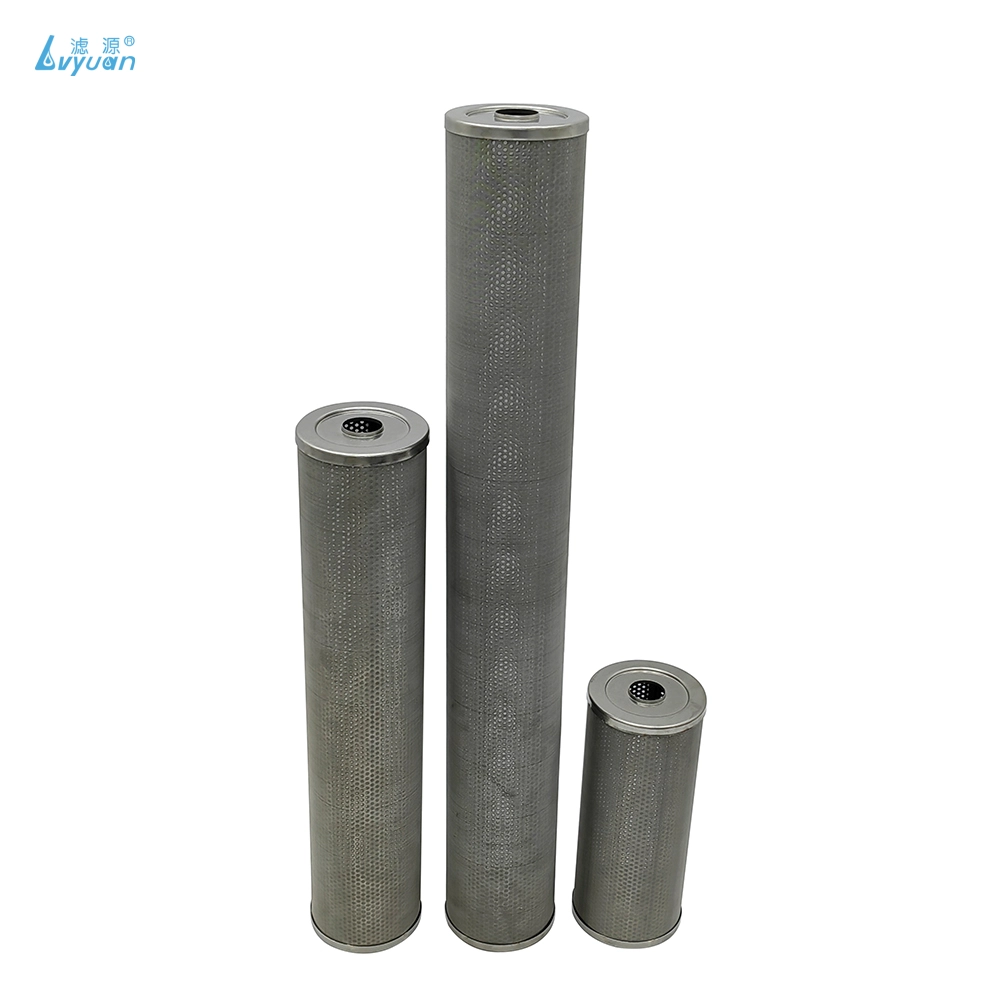
What Are Sintered Metal Filters and How Do They Work?
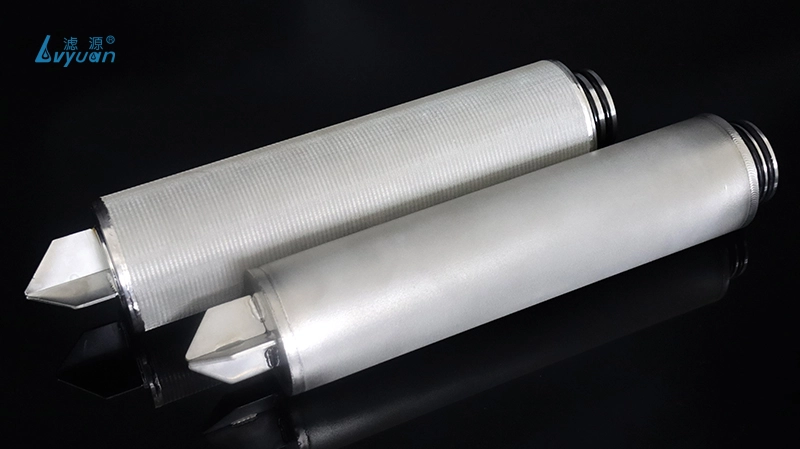
5 Benefits of Using Titanium Filters for Filtration
Metal mesh filters
What types of contaminants can sintered wire mesh filter?
Sintered wire mesh can filter a wide range of contaminants, including particles, solids, and impurities from liquids and gases. The filtration efficiency depends on factors such as pore size and material selection.
For company
Lvyuan main product advantages
• Quality Assurance:
Lvyuan prioritizes quality as a cornerstone of its operations. We adhere to rigorous quality control standards throughout the manufacturing process to ensure that our products meet the highest industry standards.
• Innovative Technology:
We leverage cutting-edge technologies in the design and production of our products. By staying at the forefront of technological advancements, we provide our customers with innovative solutions that meet their evolving needs.
• Diverse Product Range:
Lvyuan offers a comprehensive and diverse range of products, catering to various industries and applications. Our extensive product portfolio allows customers to find solutions tailored to their specific requirements.
• Customization Capabilities:
Recognizing the unique needs of our customers, we provide customizable options for our products. This ensures that our clients receive tailored solutions that align with their individual preferences and applications.
• Competitive Pricing:
We are committed to offering competitive prices without compromising on quality. Our cost-effective solutions enable customers to access high-quality products at reasonable and competitive market rates.
Sintered Titanium Filters
What Applications Are Sintered Titanium Filters Suitable For?
Sintered titanium filters are versatile and find applications in water treatment, gas diffusion, chemical experiments, and pharmaceutical processes due to their temperature resistance and corrosion resilience.
Porous Plastic Filter
What are the typical applications of sintered plastic porous filters?
Sintered plastic porous filters are used in various industries, such as pharmaceuticals, food and beverage, water treatment, automotive, aerospace, and electronics, for filtration, separation, venting, and fluidization applications.
Stainless Steel Cartridge Filter Housing
What are the benefits of using stainless steel cartridge filter housings?
Stainless steel cartridge filter housings offer corrosion resistance, durability, and hygiene, making them suitable for use in a wide range of industries, including food and beverage, pharmaceuticals, chemicals, and water treatment.
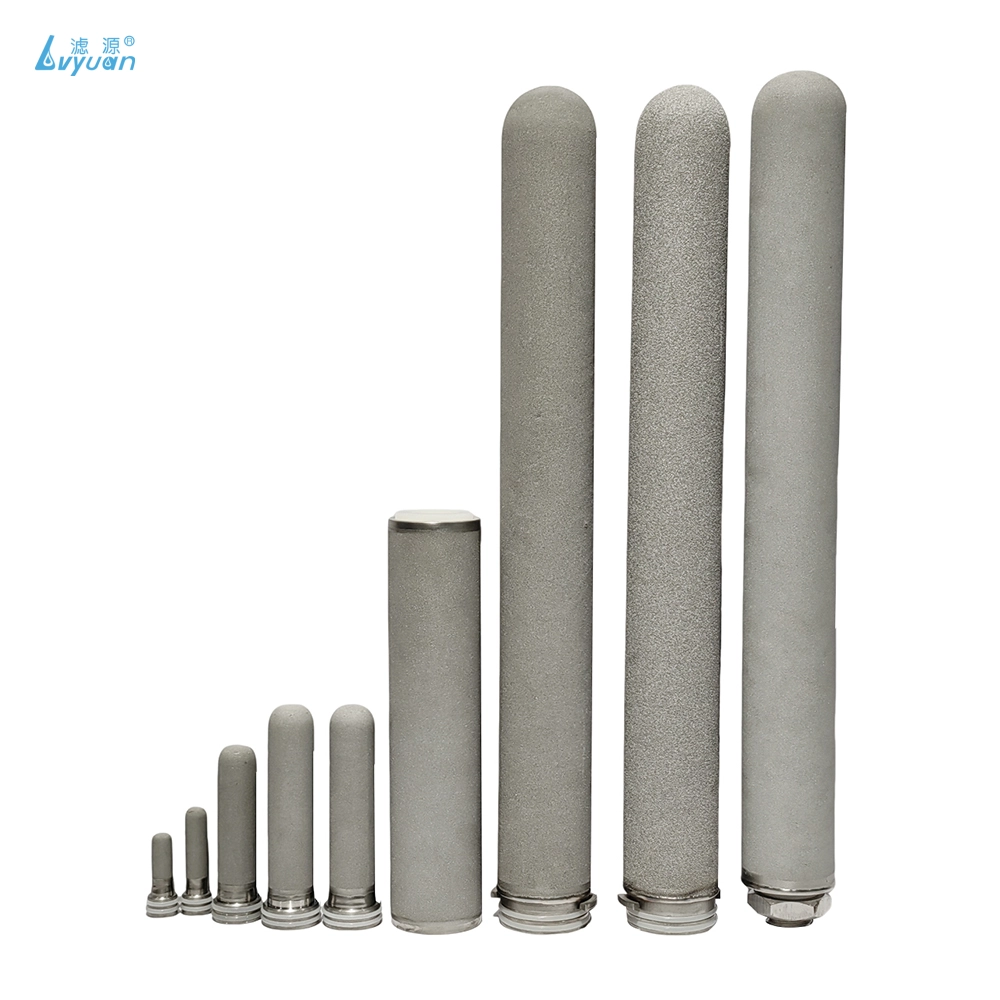
Sintered powder metal filters
Sintered powder metal filters are crafted from compressed and sintered metal powders, forming a porous structure. Porosity: 28%-50% Permeability: 0.02-20L/cm²minPa Pressure Resistance: 0.5Mpa Temperature Resistance: Less than 280℃
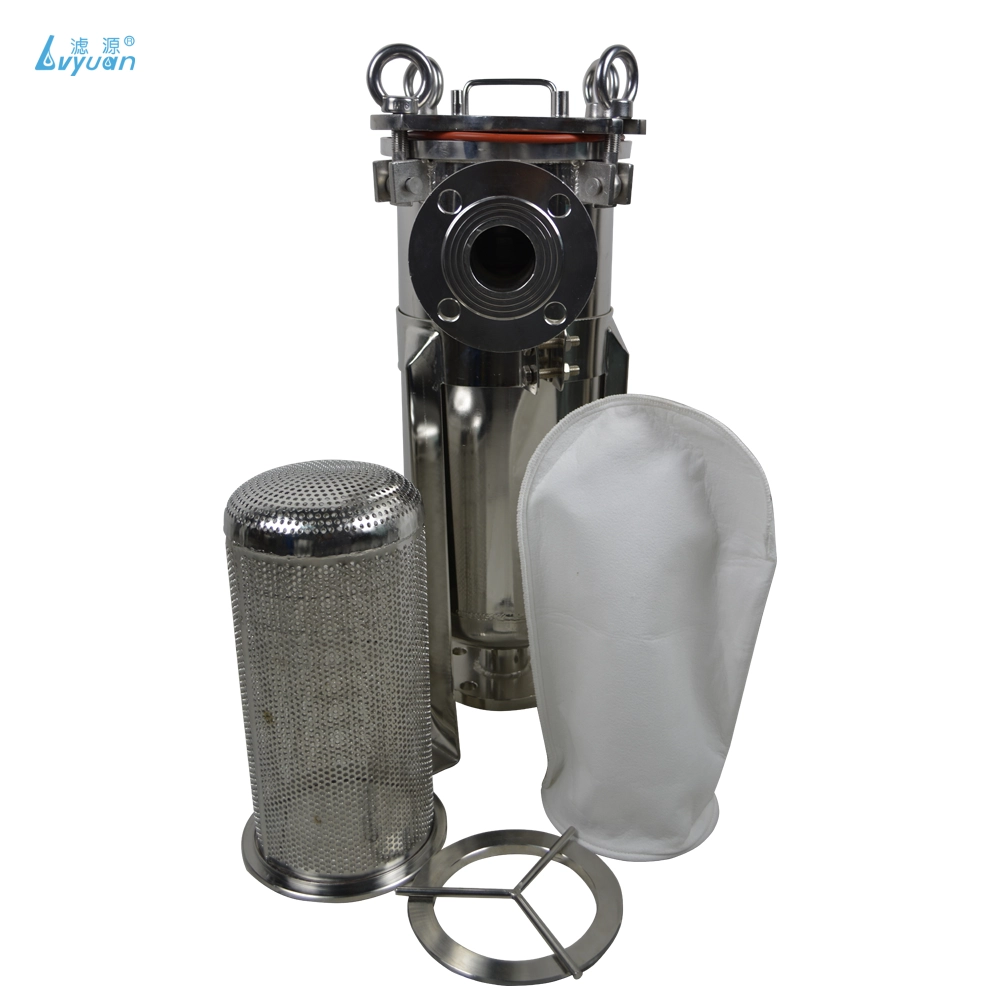
Bag filter housing
Bag filter housings are essential components in industrial filtration systems, designed to remove contaminants from liquids. To enhance the functionality and efficiency of bag filter housings, various features can be incorporated.
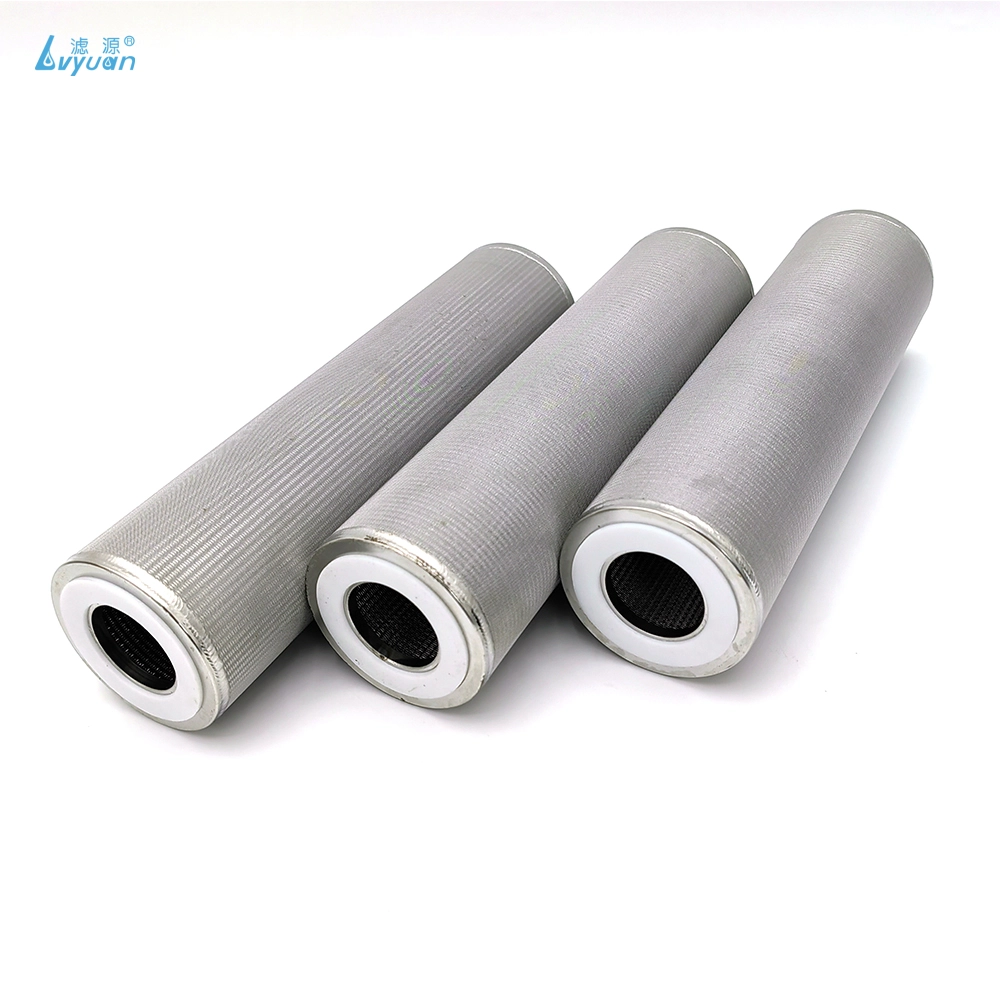
Sintered wire mesh filter
Benefit from outstanding high-pressure resistance and consistent filtration efficiency with Lvyuan's sintered metal mesh. Our sintered wire mesh finds versatile applications in diffuser screens, centrifuges, breather vents, fluidized beds, chromatography, polymer processing, petrochemical industries, hydraulic filters, and more.
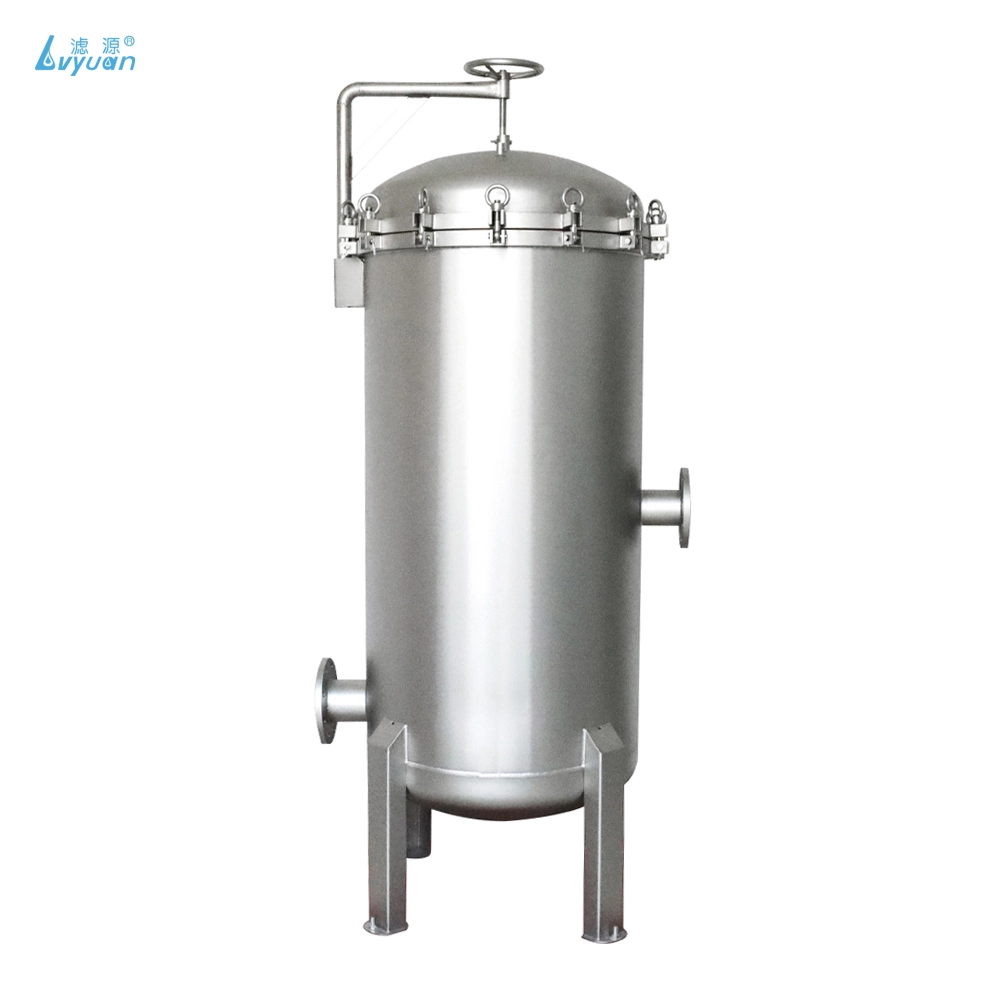
Stainless steel multi cartridge filter housing
Discover unparalleled filtration efficiency with our Stainless Steel Multi Cartridge Filter Housing – a testament to precision engineering and reliability.
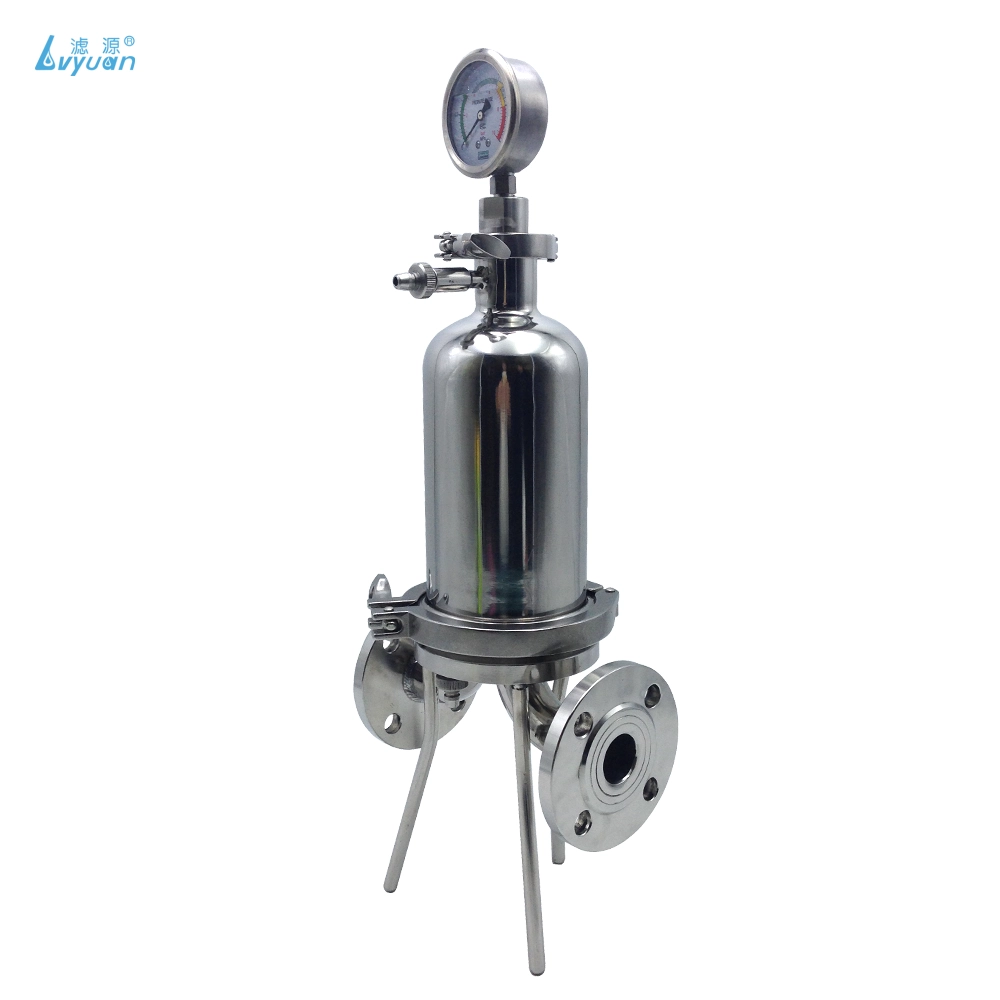
Sanitary filter housing
This filter housing will allow you to filter large volumes of nanoemulsion with ease. Sanitary vent and drain valves permit easy venting, draining, sampling, or integrity testing operations. The new cartridge locking design features additional cut-outs for traditional half-moon portions of the Code 7 bayonet locks, enhancing clean ability and drain ability.
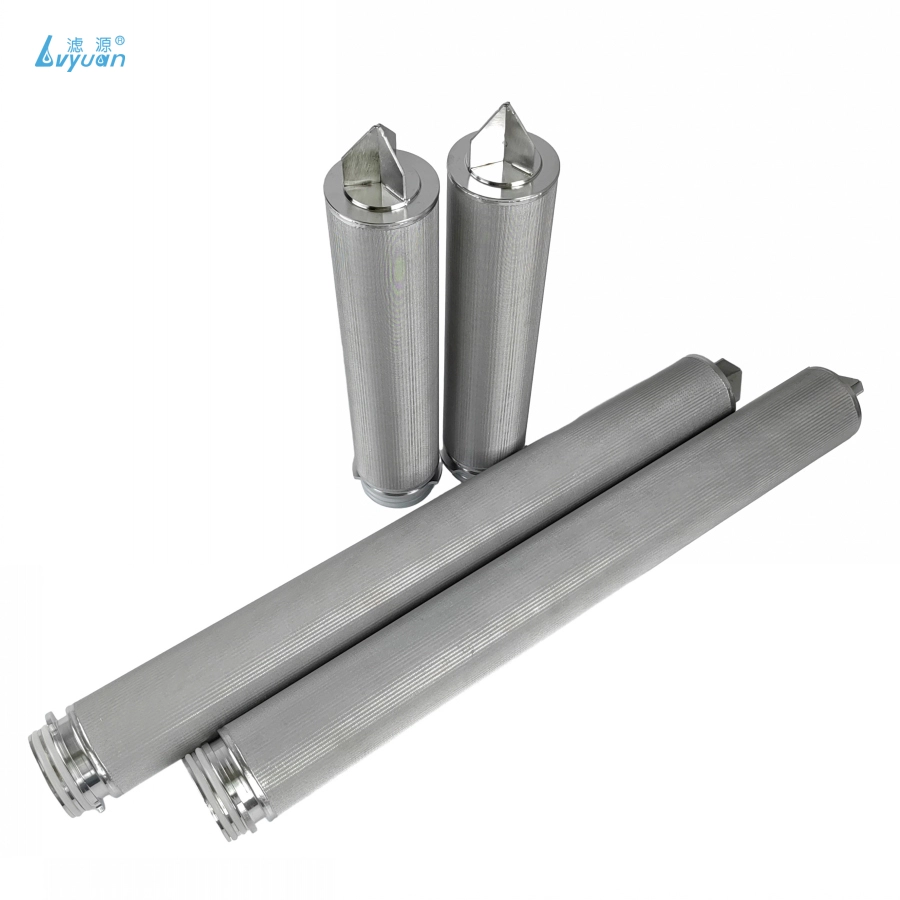
stainless steel filter water
Lvyuan’s sintered stainless steel filter stands as a pivotal filtration element crafted through a meticulous sintering process, with stainless steel serving as the core material.
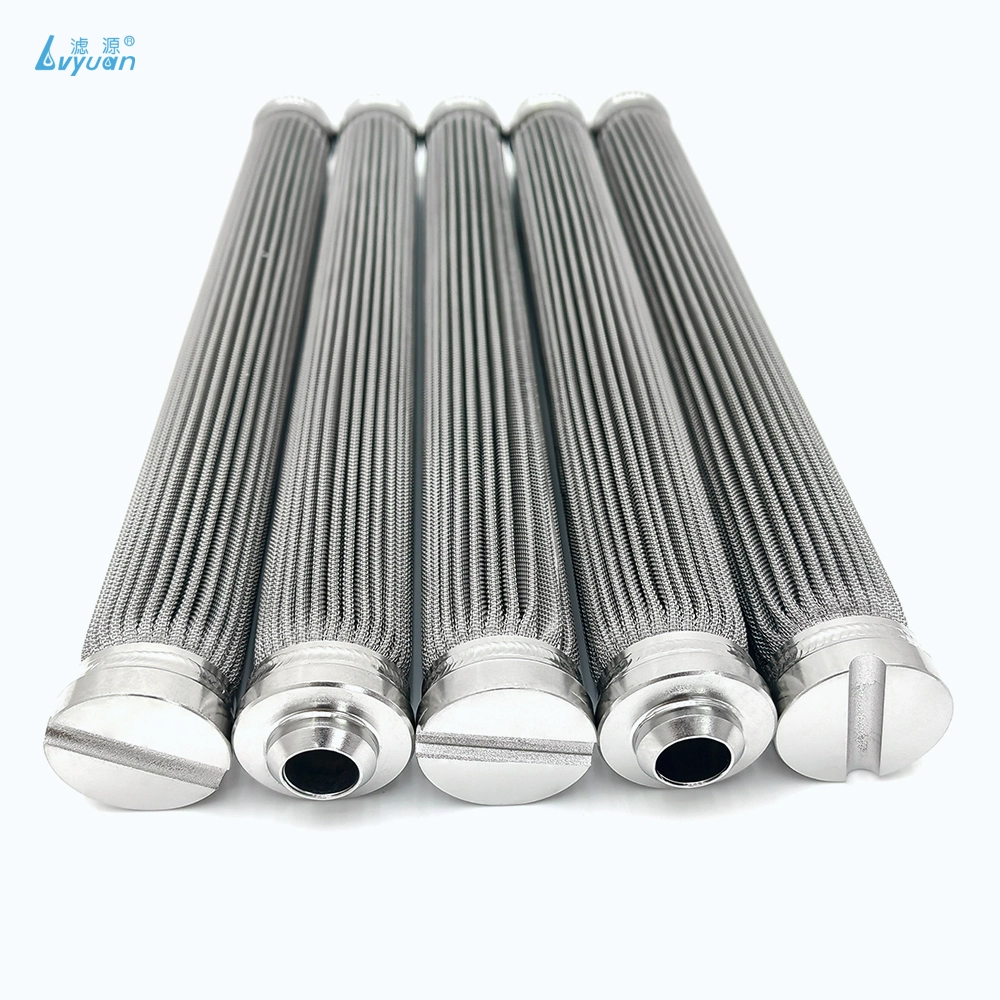
Stainless steel pleated filter cartridge
Lvyuan Stainless Steel Pleat Filter Cartridge constructed from high-quality SS 304 or SS 316L material, this filter exhibits exceptional resistance to high temperatures and rust.
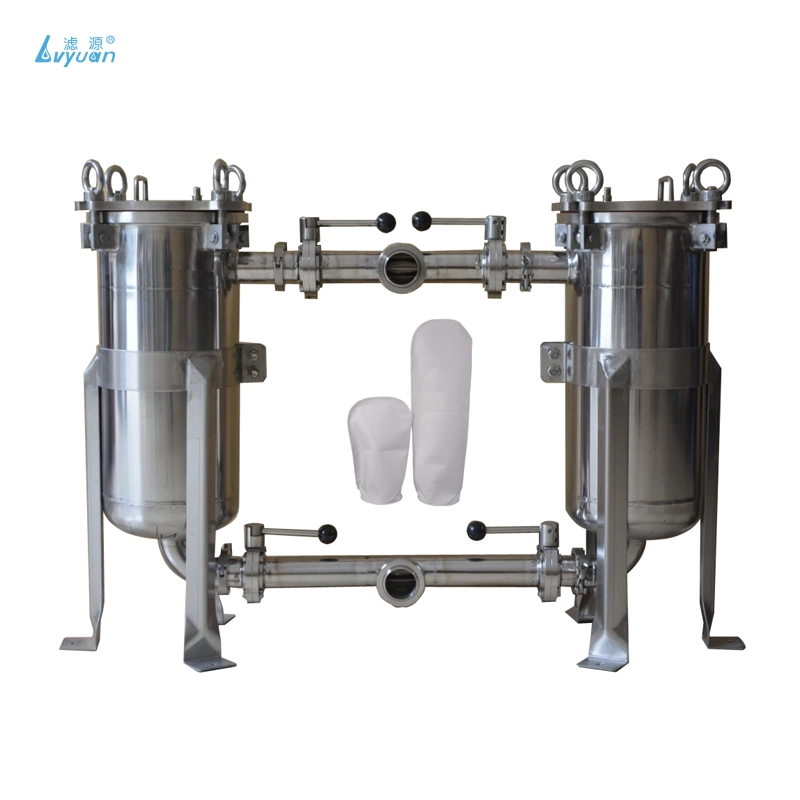
Stainless Steel Duplex filter housing
As the manufacturer, we offer a comprehensive range of Duplex Filter Housings designed to provide efficient and reliable filtration solutions for various industrial applications.
© 2024 Lvyuan All Rights Reserved. | Privacy policy • Terms and conditions