Research into porous metal filters: Characteristics, Applications and Future Innovations
Porous metal filters are an exceptional group of materials that have transformed many industries, including aerospace and healthcare. Due to their unique combination of properties, porous metal filters play an essential role in systems that require excellent efficiency along with durable performance and precise operation. This article explores porous metal materials by examining their basic concepts, along with their different types and properties, benefits, production methods, applications, and potential future uses.
- What are porous metal materials?
- The types of porous metal materials
- Properties of porous metal materials
- The manufacturing process of porous metal materials
- The advantages and disadvantages of porous metal materials
- Advantages
- Disadvantages
- The applications of porous metal filters
- The future of porous metal materials
- Conclusion
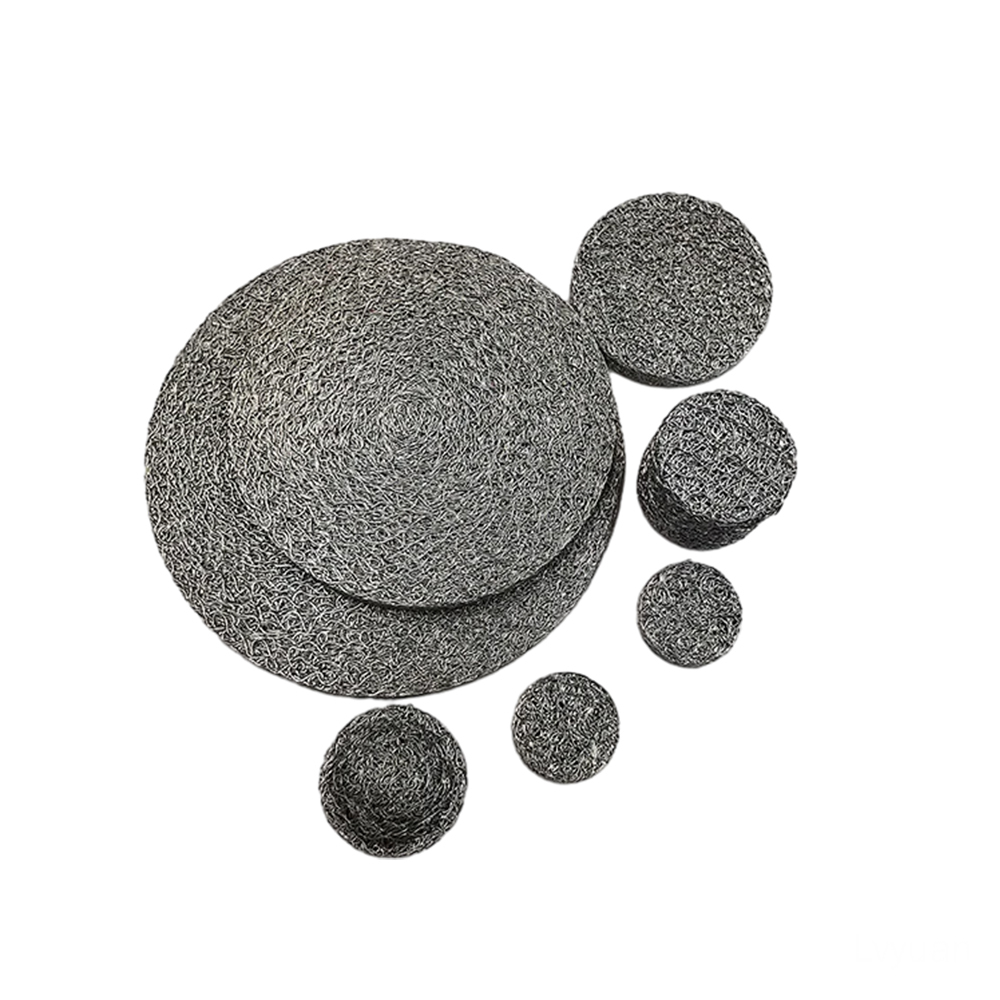
What are porous metal materials?
Porous metal materials consist of metals with engineered interconnected pores that combine metal strength with filtration capabilities. Porous metal materials allow fluids and gases to flow while trapping solids, making them ideal for filtration as well as separation and energy absorption applications.
The unique design of porous metal filters allows them to operate effectively in harsh conditions, including both elevated temperatures and corrosive environments. Industry chooses porous metal filters because they outperform conventional filtration systems. This section explains the different classifications of porous metal materials.
The types of porous metal materials
Various forms of porous metal materials are available to meet different application requirements. The most common types include:
Metal foams: The specific properties of metal foams include lightweight construction and high porosity, making them suitable for thermal management and energy absorption applications.
Sintered Metal Filters: The manufacturing process for metal filters involves compacting metal powders and then heating them to achieve both precise filtration and high mechanical strength.
Wire mesh filters: The woven metal wire structure of these filters makes them suitable for coarse filtration applications in industrial metal filters.
The different types of filters have specific characteristics to meet particular environmental requirements. For example, stainless steel and nickel alloys are used for high-temperature metal filters because they can withstand intense heat.
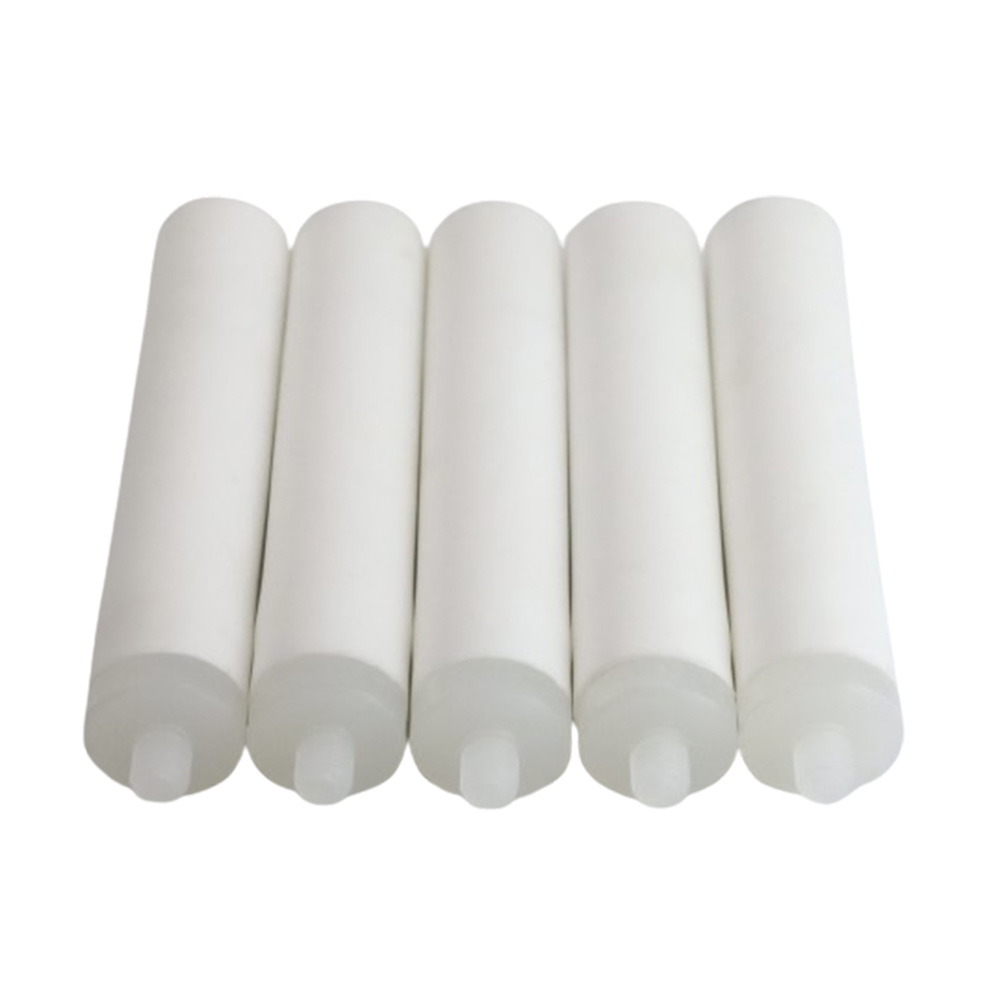
Properties of porous metal materials
The unique properties of porous metal materials differentiate them from alternative filtration methods. Key characteristics include:
High porosity: The interconnected pores of this material create a system that allows fluids or gases to flow while trapping contaminants.
Thermal and chemical resistance: Porous metal filters have thermal and chemical resistance due to the use of stainless steel and titanium materials.
Customization: The pore size and structure of these materials can be tailored to meet specific requirements, making them suitable for a wide range of applications.
The properties of porous metal materials make them an ideal choice for businesses that require precise, durable solutions.
The manufacturing process of porous metal materials
The manufacture of porous metal filters requires a variety of advanced manufacturing techniques, including:
Powder Metallurgy: The powder metallurgy process begins by compacting metal powders before sintering them to form a porous structure.
Foaming: The introduction of gas into molten metal produces a foamy structure.
3D printing: Additive manufacturing enables highly customized designs.
Manufacturing techniques produce filters with exact pore sizes and shapes to meet specific industrial requirements. For example, the pharmaceutical industry requires precise filters, so porous metal filter manufacturers use powder metallurgy manufacturing techniques.
The advantages and disadvantages of porous metal materials
Porous metal filters, like all materials, have both advantages and disadvantages.
Advantages
Durability: Materials demonstrate resistance to high pressures, temperatures, and corrosive conditions.
Reusability: Porous metal filters demonstrate reusability by allowing cleaning for multiple uses.
Efficiency: Porous metal filters maintain high filtration accuracy due to their precise pore structure design.
Disadvantages
Cost: Custom porous metal filters are expensive to manufacture.
Weight: Some types, such as metal foams, can be heavier than polymer-based filters.
Understanding these advantages and disadvantages is crucial to choosing the right filter for you.
The applications of porous metal filters
Porous metal filters have versatility that allows them to be used in many different applications. Porous metal filters are used in a variety of applications, including:
Aerospace: The aerospace industry uses high-temperature metal filters to remove contaminants from the fuel and air components of jet engines.
Healthcare: Medical devices, including bone implants and drug delivery systems, use porous titanium filters in healthcare applications.
Industrial Filtration: Industrial filtration uses industrial metal filters for applications in oil and gas, chemical processing, and water treatment.
Energy: These materials improve energy efficiency in fuel cells and batteries.
The wide range of applications demonstrates the importance of porous metal filters in today's technological developments and industrial processes.
The future of porous metal materials
Porous metal materials will continue to be the focus of research efforts as scientists look for improvements in properties and new applications. Innovations in nanotechnology and additive manufacturing will lead to better and more personalized filtration systems. The growing market need for sustainable solutions has led to the development of recyclable and environmentally friendly porous metal filters.
Companies that want to stay ahead should partner with porous metal filter manufacturers that offer customized metal filter solutions.
Conclusion
Porous metal filters serve as essential engineering components since they combine exceptional reliability with high efficiency alongside incredible adaptability. The large number of applications for porous metal filters extends across the aerospace and healthcare industries, with ongoing expansion potential. The growing technological progress will expand the potential uses of these materials so they become vital elements for future developments. Before making an informed decision, you need to understand the features and applications of porous metal filters when you seek industrial metal filters or custom solutions.
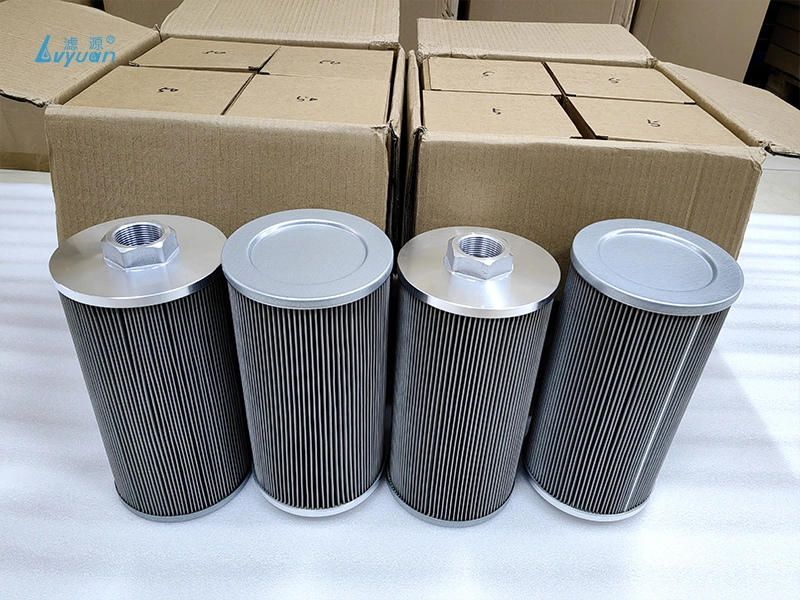
What is Sintered Metal Filter? Complete Guide by Lvyuan

Sintered PTFE Filters: Advanced Filtration for Demanding Environments
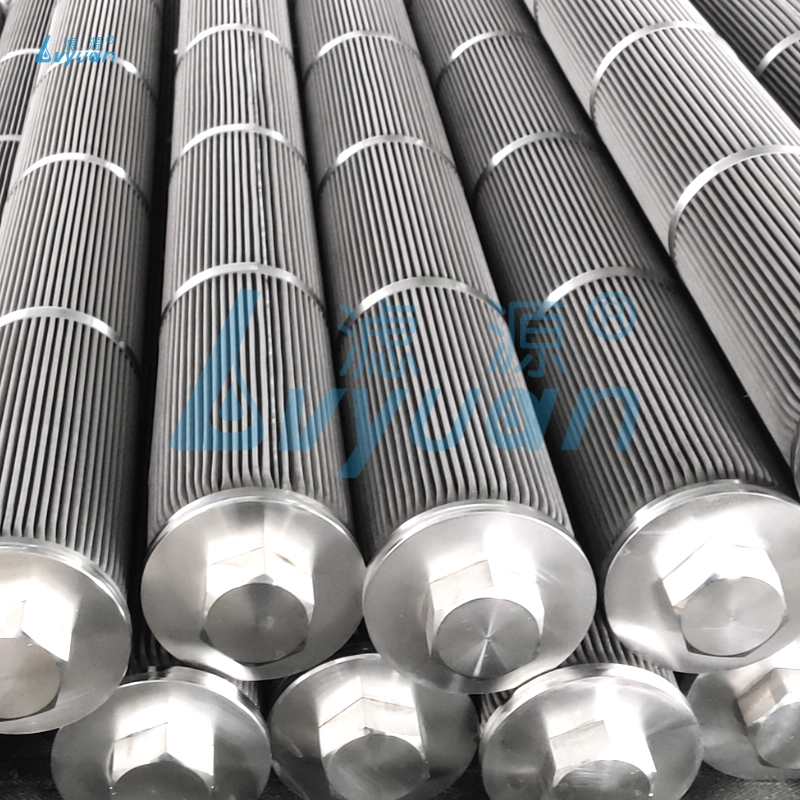
Metal Sintered Filters: Precision Filtering to Drive Industrial Upgrading
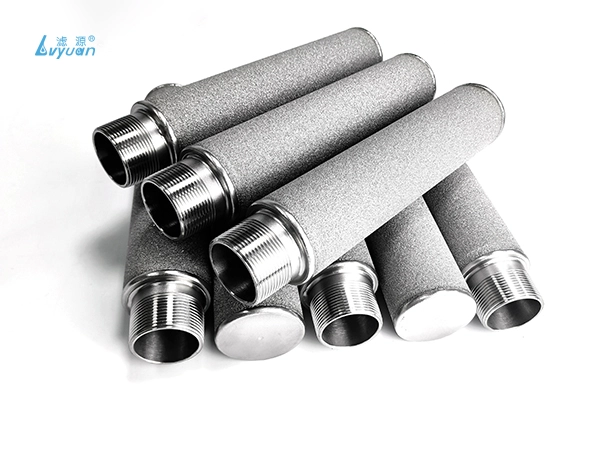
Choosing Sintered Filters: An Overview for Industrial Applications
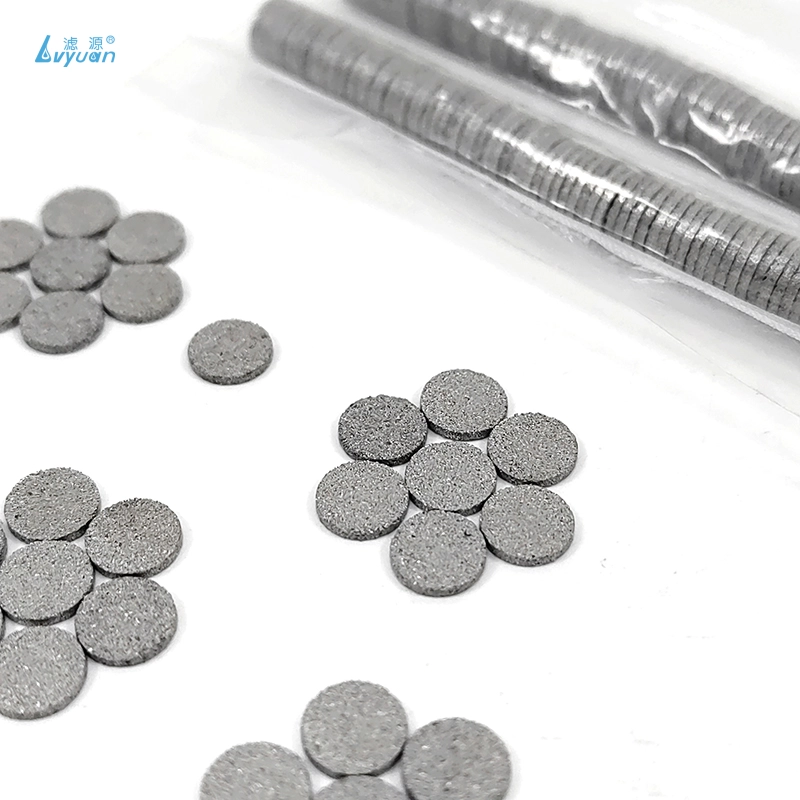
What is a Sintered Metal Filter Disc? A Comprehensive Guide
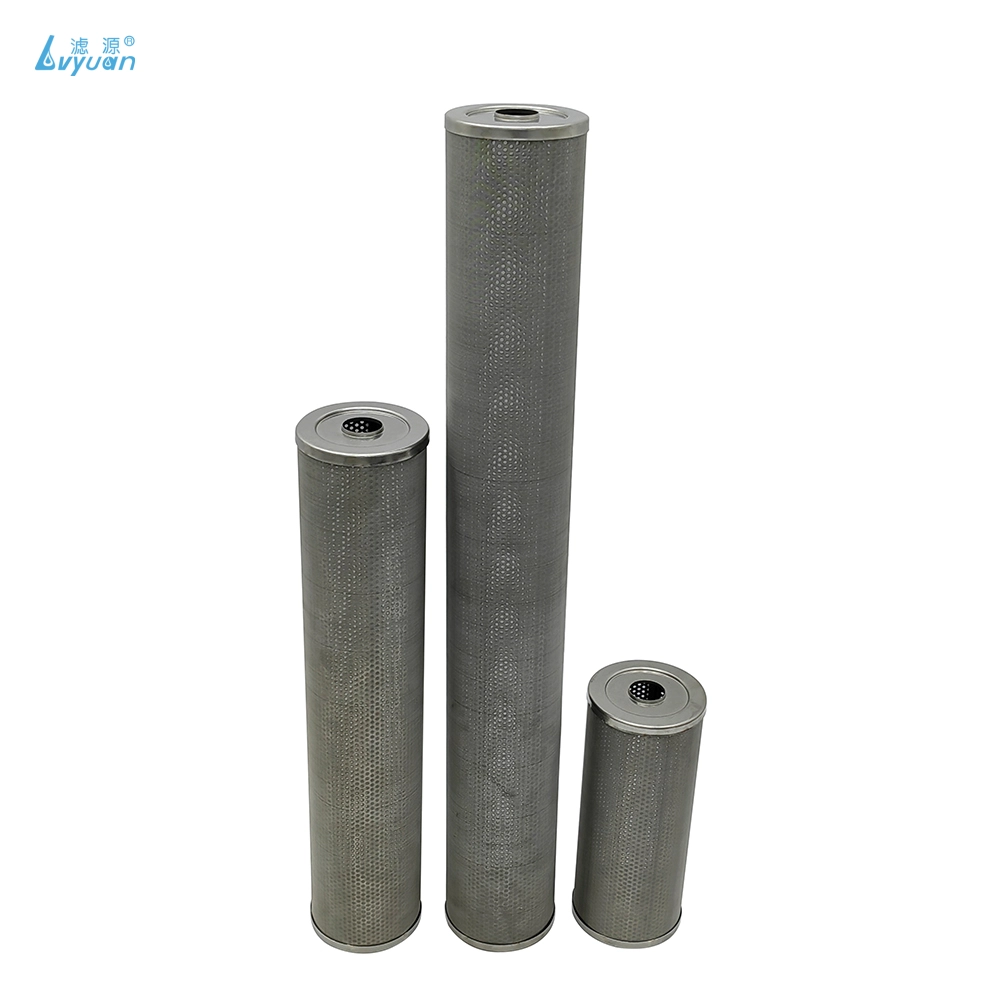
What Are Sintered Metal Filters and How Do They Work?
For customization
Do you test all your goods before delivery?
Yes, we have a 100% test before delivery.
Sintered mesh filters
Can sintered mesh filters be customized for specific requirements?
Yes, sintered mesh filters are highly customizable. They can be tailored based on factors such as filtration rating, material composition (e.g., stainless steel, monel), dimensions, and shape to meet the unique needs of different applications.
What are the main applications of sintered mesh filters?
Sintered mesh filters find applications in industries such as petrochemicals, pharmaceuticals, food and beverage, aerospace, and water treatment. They are used for filtration, dispersion, fluidization, and separation processes.
Metal mesh filters
What applications is sintered wire mesh suitable for?
Sintered wire mesh filter finds applications in various industries, including:
• Filtration of liquids and gases.
• Polymer and chemical processing.
• Pharmaceutical and food processing.
• Aerospace and automotive industries.
• Environmental protection and water treatment.
Porous Plastic Filter
How to Calculate Filter Porosity?
Filter porosity is classified into three major types: Primary Porosity, Secondary Porosity, and Effective Porosity. The calculation involves determining the ratio of the volume of gaps in the filter to the total volume, expressed as a percentage.
Porosity = (Volume of Empty Gaps/Total Volume of Filter) x 100
Other methods include:
• Direct Methods: Calculate the entire volume of the porous filter and the volume of a skeletal filter (without pores) to find the porosity.
• Computed Methods: Use modern computer technology to obtain a 3D image of a porous filter and employ defect analysis techniques.
• Water Evaporation Technique: Calculate porosity by determining the difference in weight between the saturated filter in water and the dried filter.
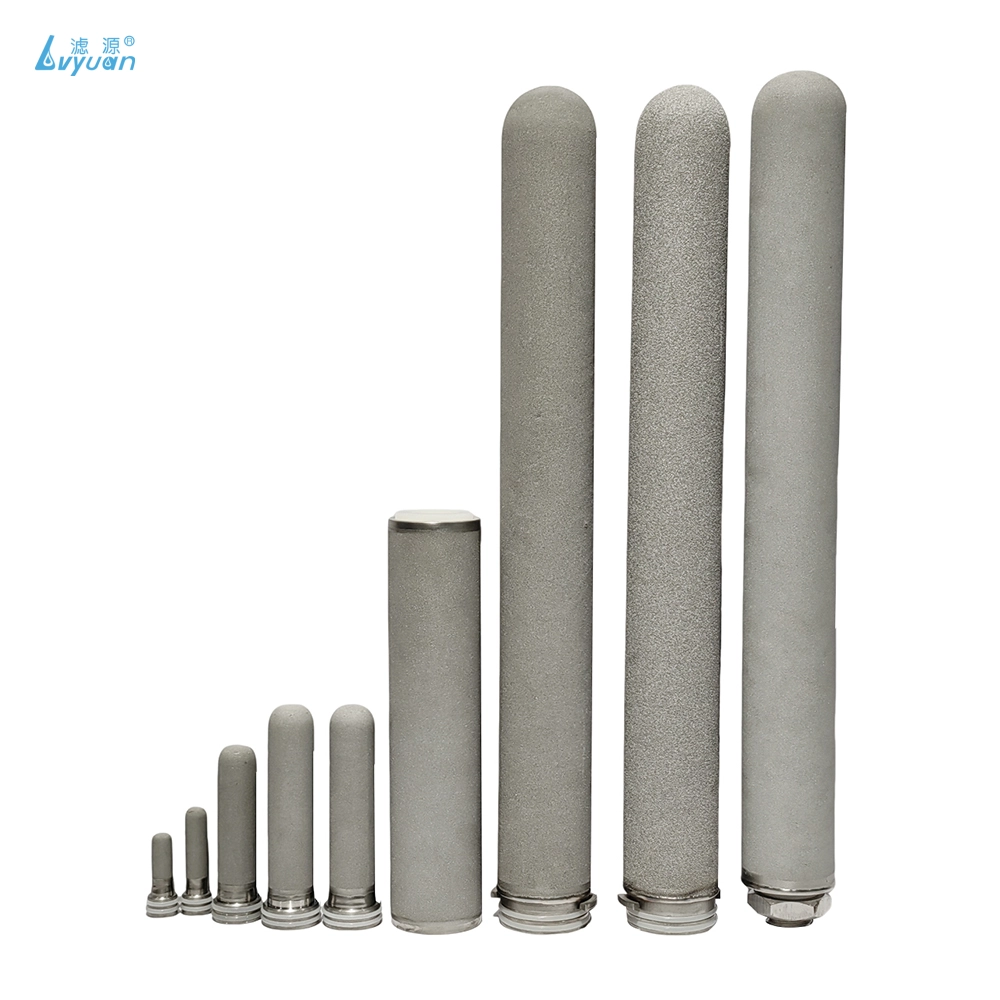
Sintered powder metal filters
Sintered powder metal filters are crafted from compressed and sintered metal powders, forming a porous structure. Porosity: 28%-50% Permeability: 0.02-20L/cm²minPa Pressure Resistance: 0.5Mpa Temperature Resistance: Less than 280℃
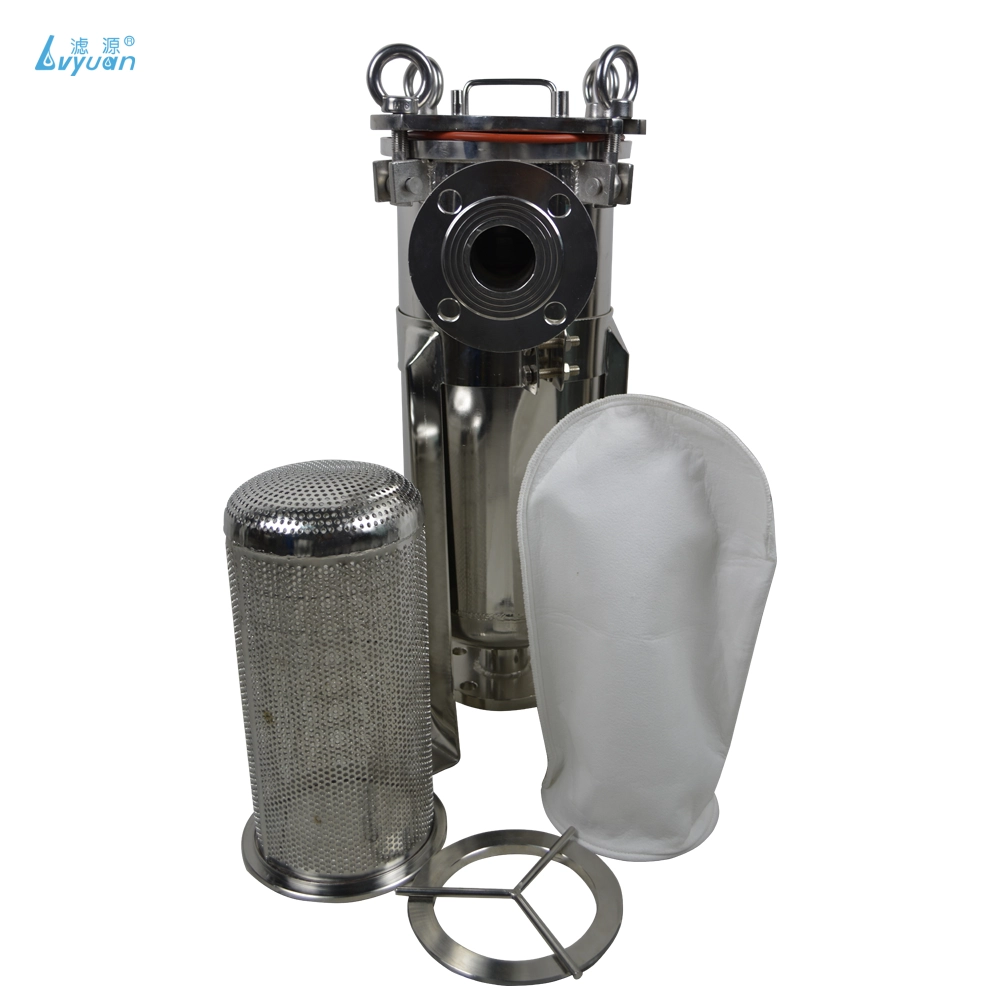
Bag filter housing
Bag filter housings are essential components in industrial filtration systems, designed to remove contaminants from liquids. To enhance the functionality and efficiency of bag filter housings, various features can be incorporated.
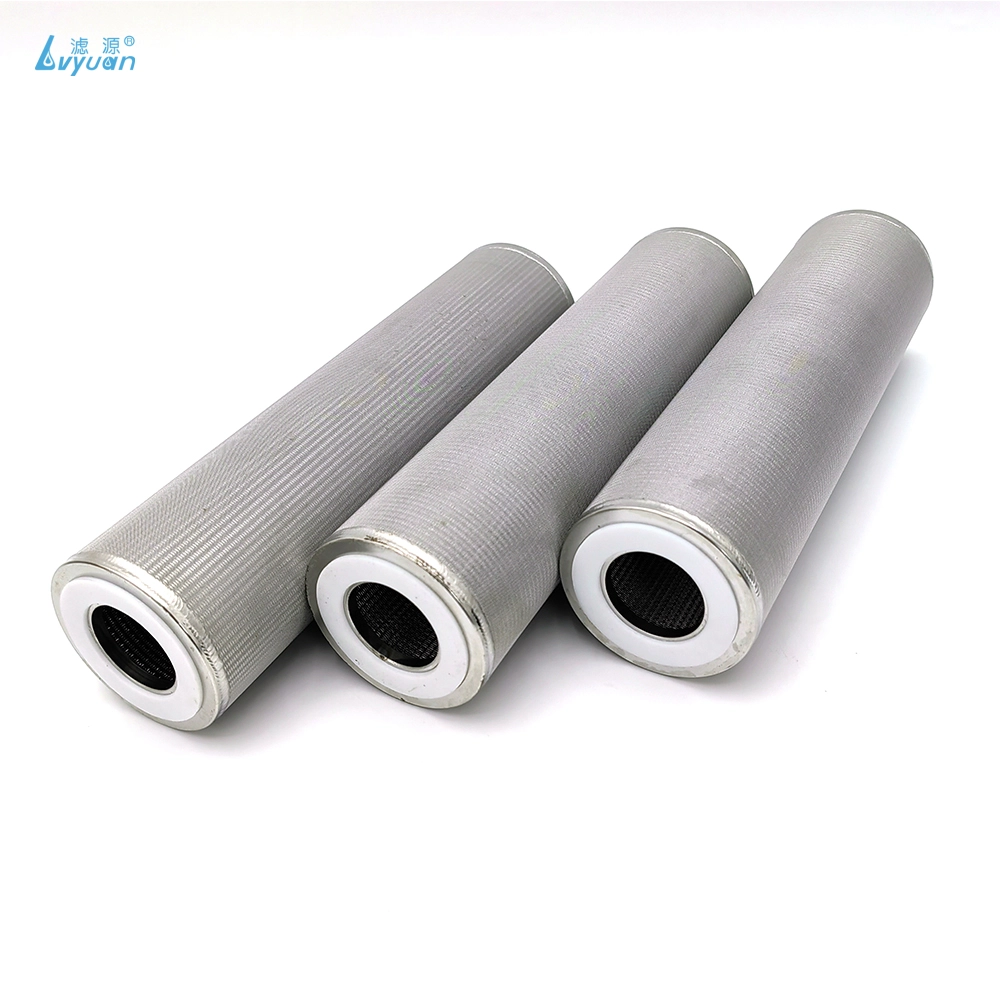
Sintered wire mesh filter
Benefit from outstanding high-pressure resistance and consistent filtration efficiency with Lvyuan's sintered metal mesh. Our sintered wire mesh finds versatile applications in diffuser screens, centrifuges, breather vents, fluidized beds, chromatography, polymer processing, petrochemical industries, hydraulic filters, and more.
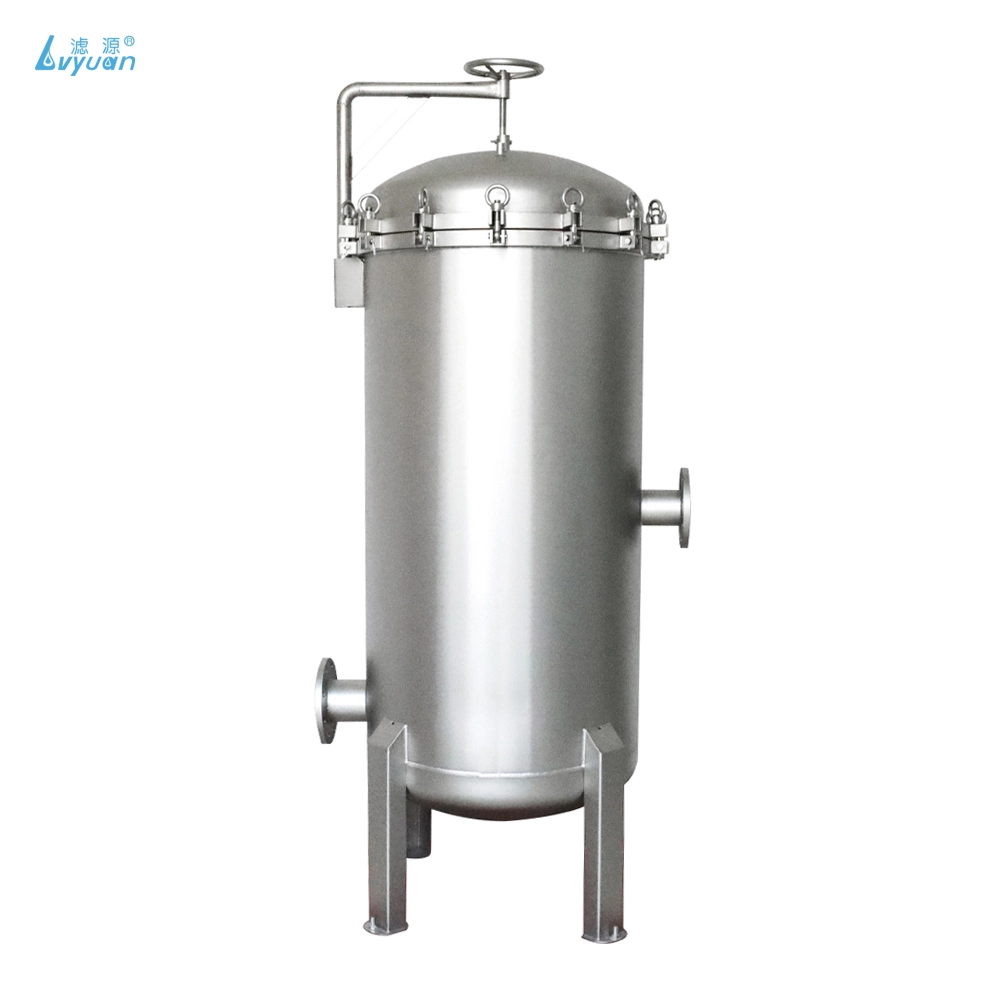
Stainless steel multi cartridge filter housing
Discover unparalleled filtration efficiency with our Stainless Steel Multi Cartridge Filter Housing – a testament to precision engineering and reliability.
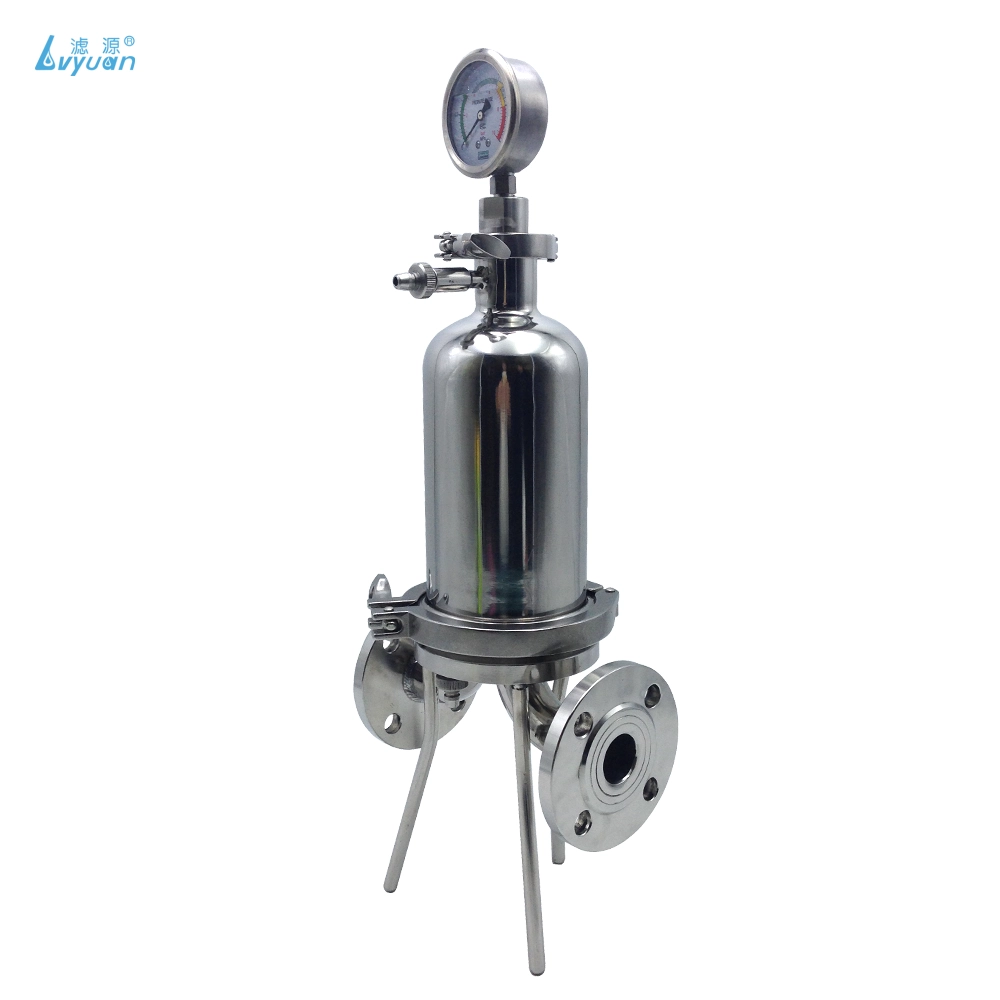
Sanitary filter housing
This filter housing will allow you to filter large volumes of nanoemulsion with ease. Sanitary vent and drain valves permit easy venting, draining, sampling, or integrity testing operations. The new cartridge locking design features additional cut-outs for traditional half-moon portions of the Code 7 bayonet locks, enhancing clean ability and drain ability.
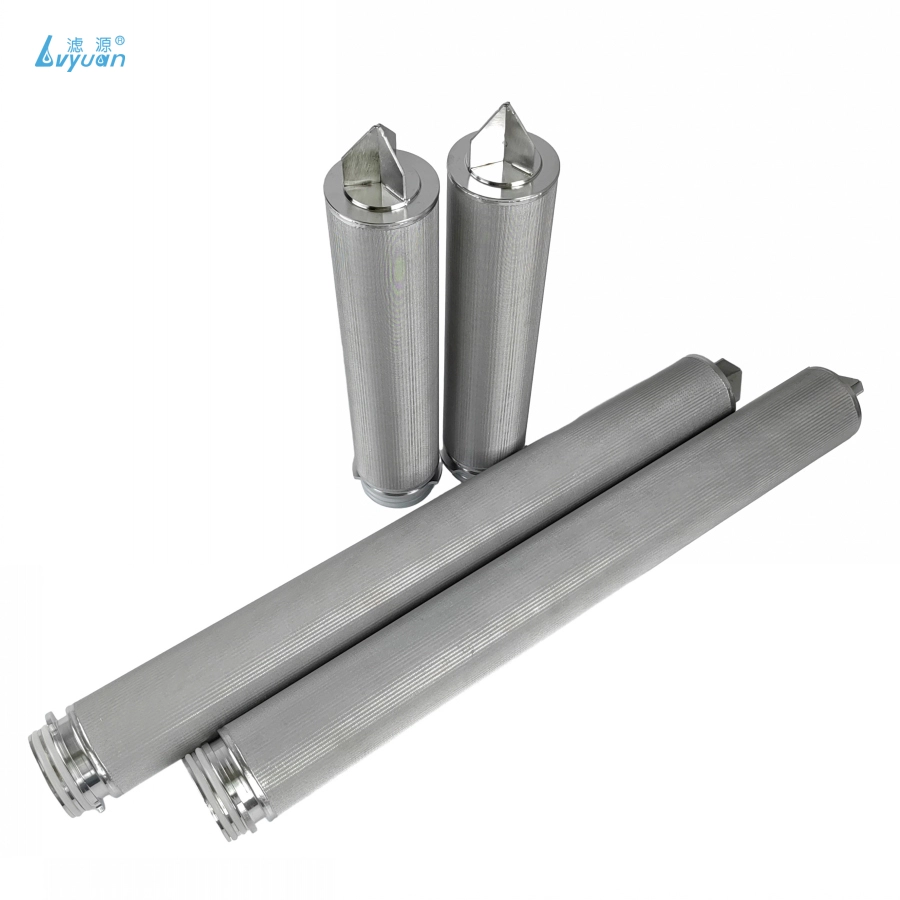
stainless steel filter water
Lvyuan’s sintered stainless steel filter stands as a pivotal filtration element crafted through a meticulous sintering process, with stainless steel serving as the core material.
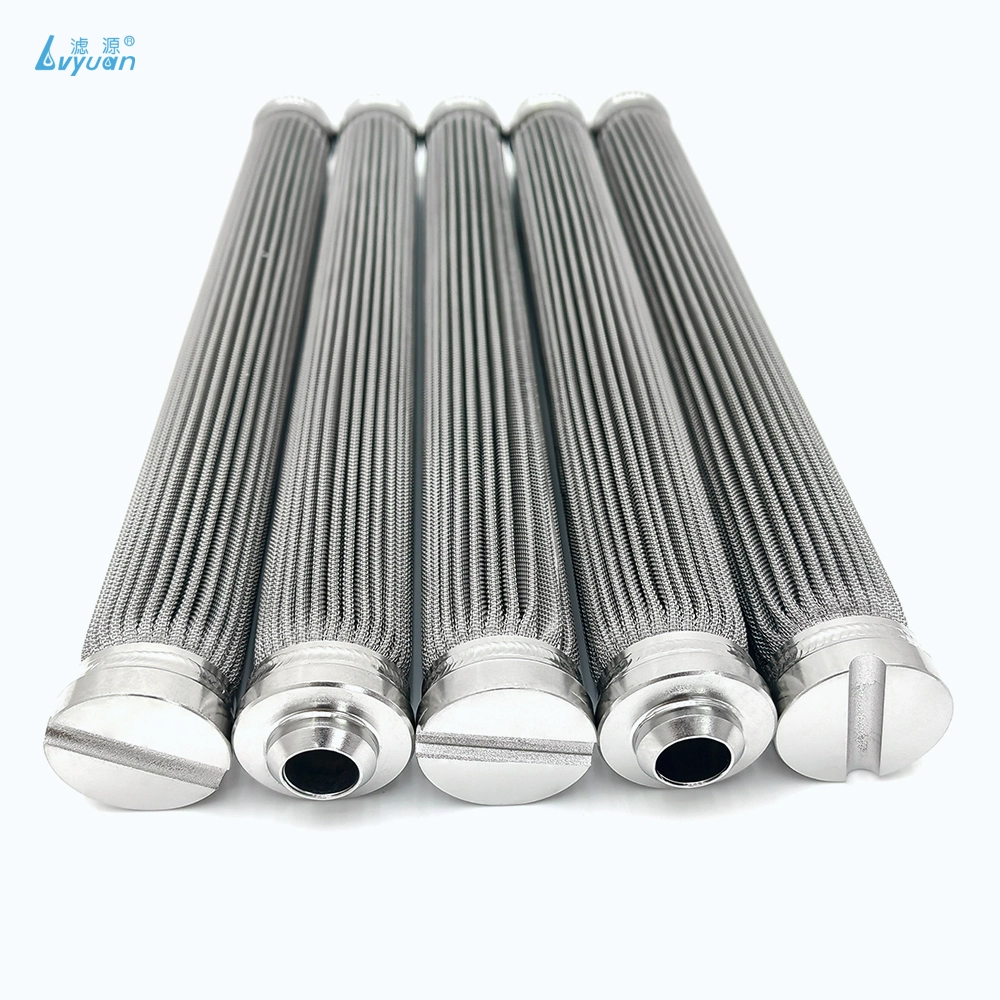
Stainless steel pleated filter cartridge
Lvyuan Stainless Steel Pleat Filter Cartridge constructed from high-quality SS 304 or SS 316L material, this filter exhibits exceptional resistance to high temperatures and rust.
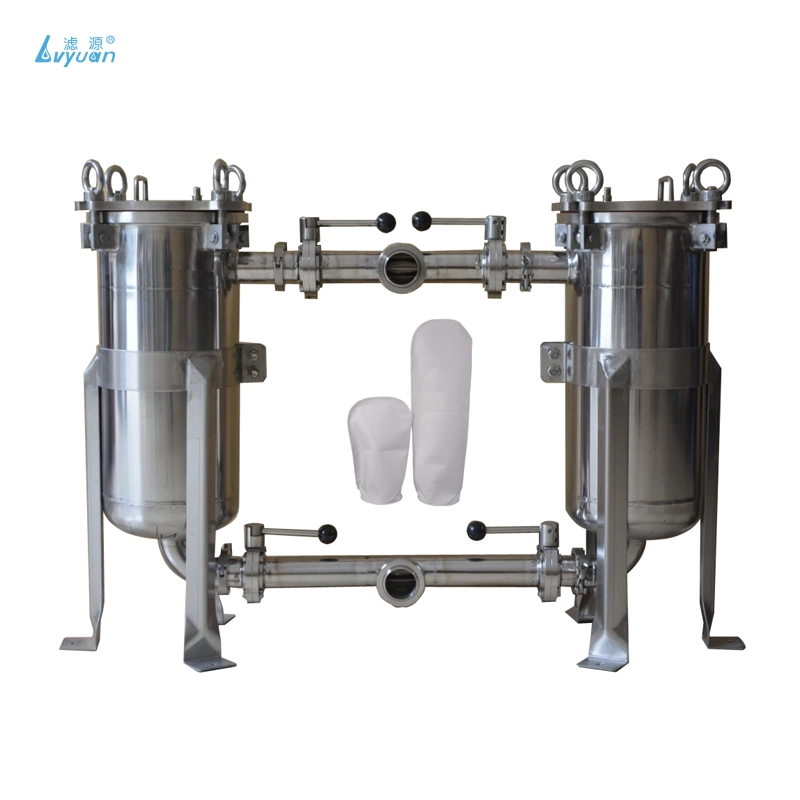
Stainless Steel Duplex filter housing
As the manufacturer, we offer a comprehensive range of Duplex Filter Housings designed to provide efficient and reliable filtration solutions for various industrial applications.
© 2024 Lvyuan All Rights Reserved. | Privacy policy • Terms and conditions