how to cut stainless steel wire mesh | Lvyuan Guide
Cutting stainless steel wire mesh accurately is critical for sintered metal filter production. This guide details methods including shearing, laser cutting, waterjet cutting, and EDM, highlighting factors influencing method selection like mesh thickness and desired accuracy. Safety precautions and post-cutting steps (deburring, cleaning) are emphasized. Lvyuan provides expert guidance for optimal filter production.
How to Cut Stainless Steel Wire Mesh for Sintered Metal Filters - Lvyuan
Cutting stainless steel wire mesh accurately and efficiently is crucial for creating high-quality sintered metal filters. This process demands precision to maintain the integrity of the mesh and achieve the desired filter specifications. Improper cutting can lead to damaged elements, affecting porosity and filter performance. This article provides practical guidance on the best methods.
Choosing the Right Cutting Method
* Shearing: This is often the preferred method for clean, straight cuts, particularly for thicker gauge meshes. Specialized shears designed for metal mesh minimize burring and fraying.
* Laser Cutting: Offers high precision for intricate shapes and patterns. Ideal for prototypes and complex filter designs. However, it can be costly for large-scale production.
* Waterjet Cutting: A versatile option for various thicknesses and materials. Minimizes heat-affected zones, making it suitable for heat-sensitive alloys.
* Wire EDM (Electrical Discharge Machining): Provides exceptional accuracy, especially for intricate geometries and hard-to-cut materials. Ideal for intricate filter designs.
Factors Influencing Cutting Method Selection
* Mesh Thickness: Thicker meshes may require shearing or waterjet cutting, while thinner ones can be cut with lasers or even sharp scissors (for very thin meshes only).
* Mesh Material: The specific stainless steel grade impacts the cutting method's effectiveness. High-strength alloys may necessitate waterjet or EDM cutting.
* Desired Accuracy: Laser and EDM cutting provide superior accuracy for complex filter designs.
* Production Volume: Shearing is cost-effective for mass production, whereas laser and waterjet cutting are more suitable for smaller batches or prototypes.
Safety Precautions
* Personal Protective Equipment (PPE): Always wear safety glasses, gloves, and appropriate respiratory protection when cutting stainless steel wire mesh to prevent injuries from sharp edges and airborne particles.
* Proper Tool Handling: Follow the manufacturer's instructions for each cutting tool.
* Work Area: Ensure a clean and well-lit workspace to prevent accidents.
Post-Cutting Considerations
* Deburring: After cutting, it’s crucial to deburr the edges to prevent damage to downstream processes or the finished filter. This can be done manually with a file or using automated deburring equipment.
* Cleaning: Remove any debris or cutting residue from the mesh to ensure consistent filter performance.
Conclusion
Selecting the appropriate cutting method for stainless steel wire mesh depends on several factors. Understanding these factors and following safety precautions ensures the creation of high-quality sintered metal filters that meet stringent performance requirements. Contact Lvyuan for further assistance in selecting optimal cutting techniques for your specific application.
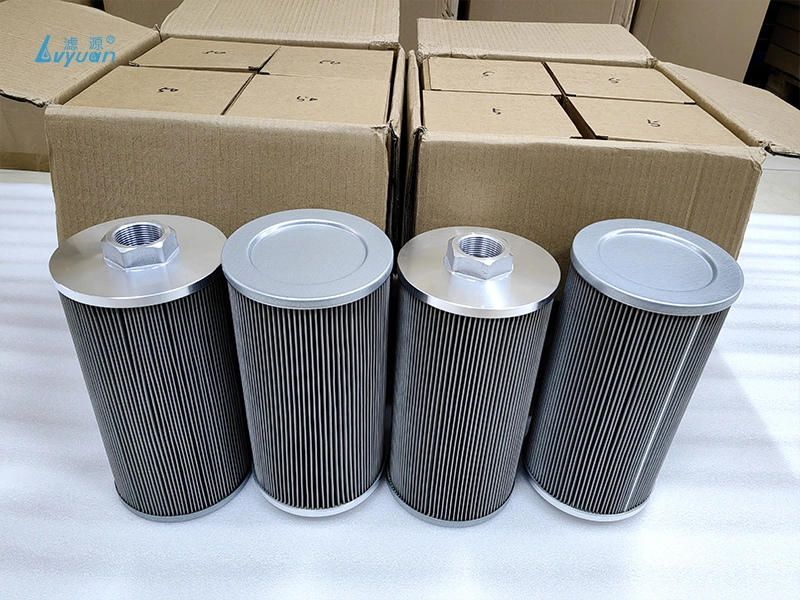
What is Sintered Metal Filter? Complete Guide by Lvyuan

Sintered PTFE Filters: Advanced Filtration for Demanding Environments
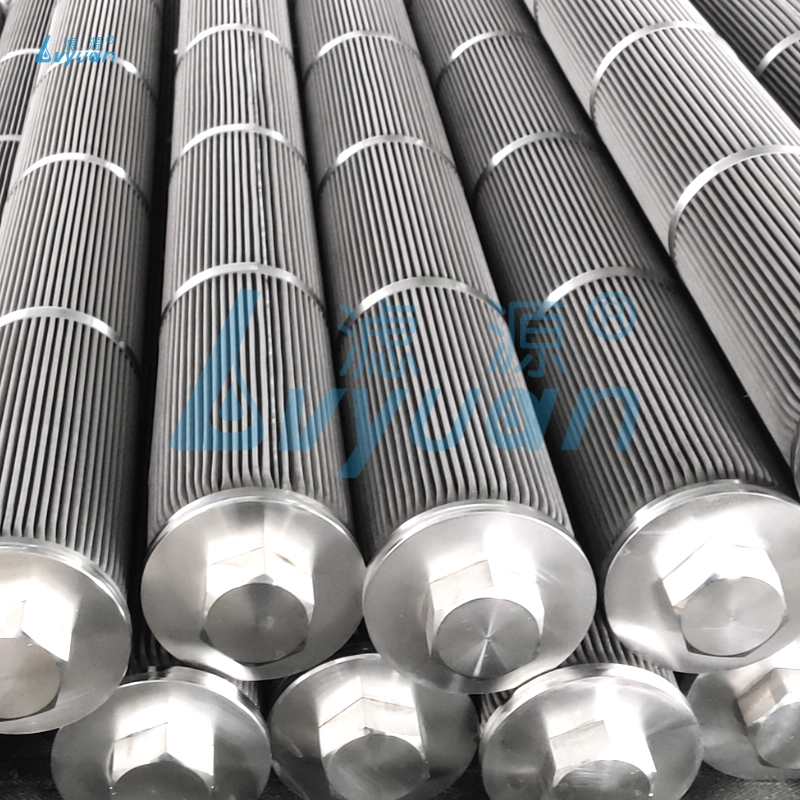
Metal Sintered Filters: Precision Filtering to Drive Industrial Upgrading
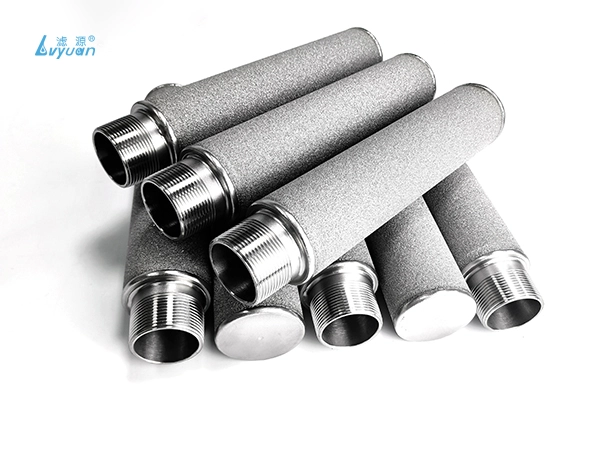
Choosing Sintered Filters: An Overview for Industrial Applications
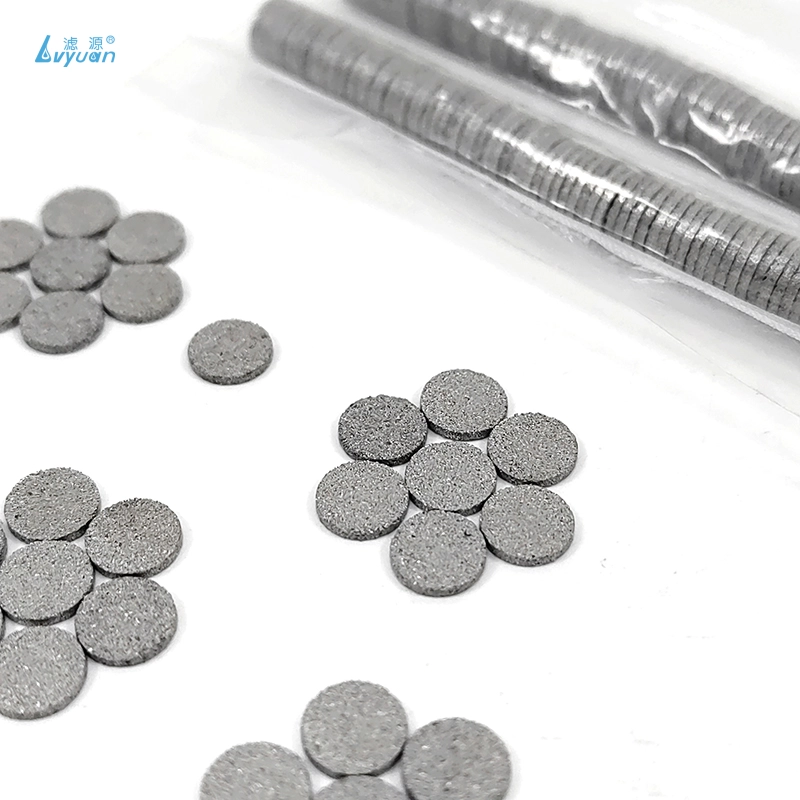
What is a Sintered Metal Filter Disc? A Comprehensive Guide
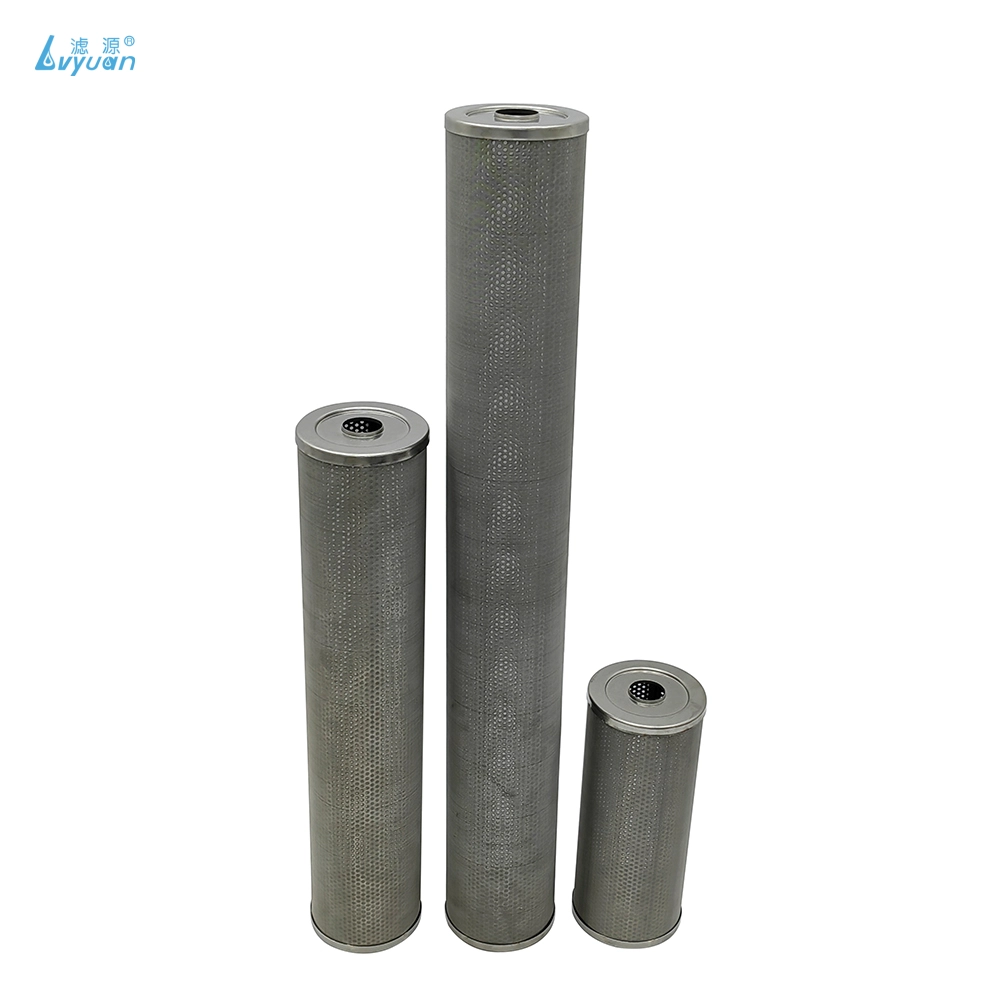
What Are Sintered Metal Filters and How Do They Work?
Sintered Titanium Filters
Are Sintered Titanium Filters Reusable?
Yes, sintered titanium filters support easy cleaning, enabling reusability and minimizing operational costs over their extended lifespan.
Sintered Metal Filter
How often should industrial sintered metal filter cartridges be replaced?
The replacement frequency depends on the operating conditions and the level of contaminants in the process. Regular inspection and monitoring help determine the optimal replacement schedule.
Stainless Steel Pleated Filter Cartridges
What are the advantages of using Stainless Steel Pleated Filter Cartridges?
Advantages include exceptional durability, high-temperature resistance, corrosion resistance, efficient filtration, versatility in applications, customization options, and cost-effectiveness.
Porous Plastic Filter
How do I integrate sintered porous filter discs into my filtration system?
They are designed for easy integration into existing filtration systems. The compact design allows for straightforward installation and replacement.
Metal mesh filters
Can sintered wire mesh filter be customized?
Yes, sintered wire mesh can be customized in terms of material, pore size, thickness, and dimensions to suit specific filtration requirements. Customization allows for optimal performance in diverse applications.
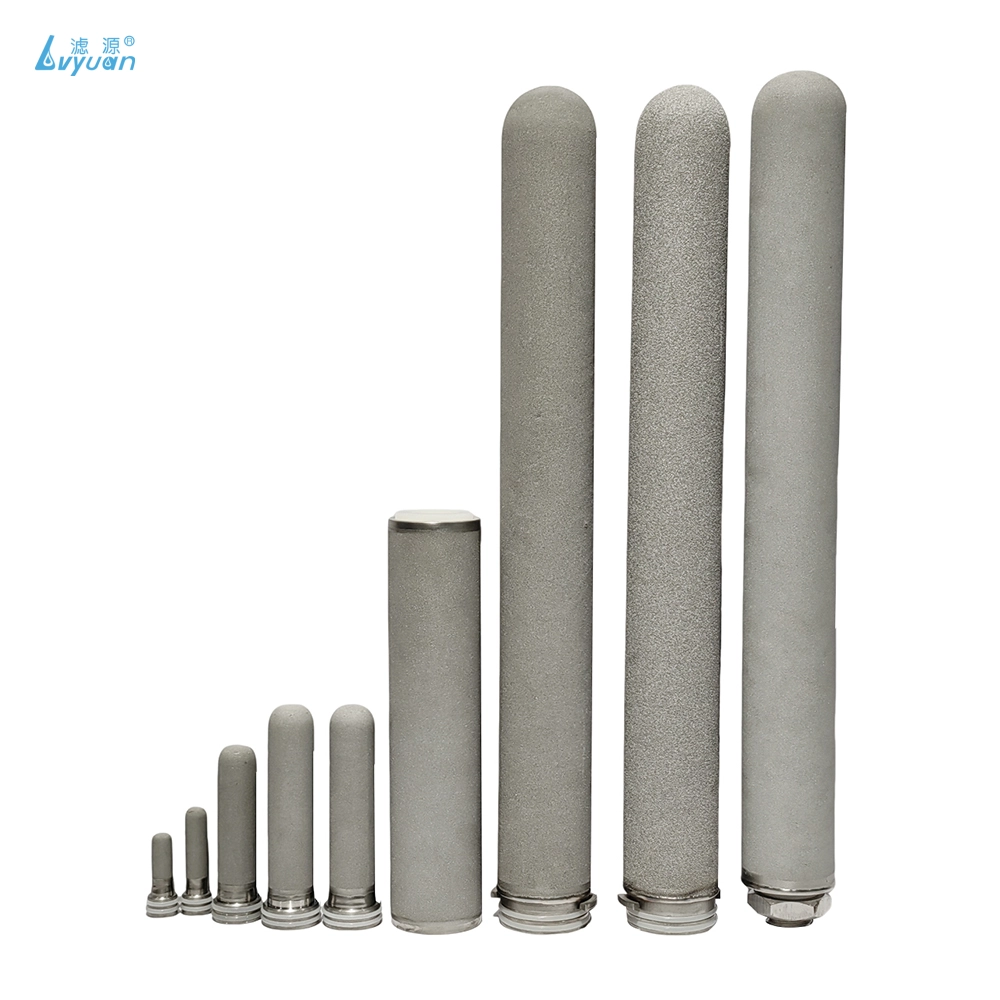
Sintered powder metal filters
Sintered powder metal filters are crafted from compressed and sintered metal powders, forming a porous structure. Porosity: 28%-50% Permeability: 0.02-20L/cm²minPa Pressure Resistance: 0.5Mpa Temperature Resistance: Less than 280℃
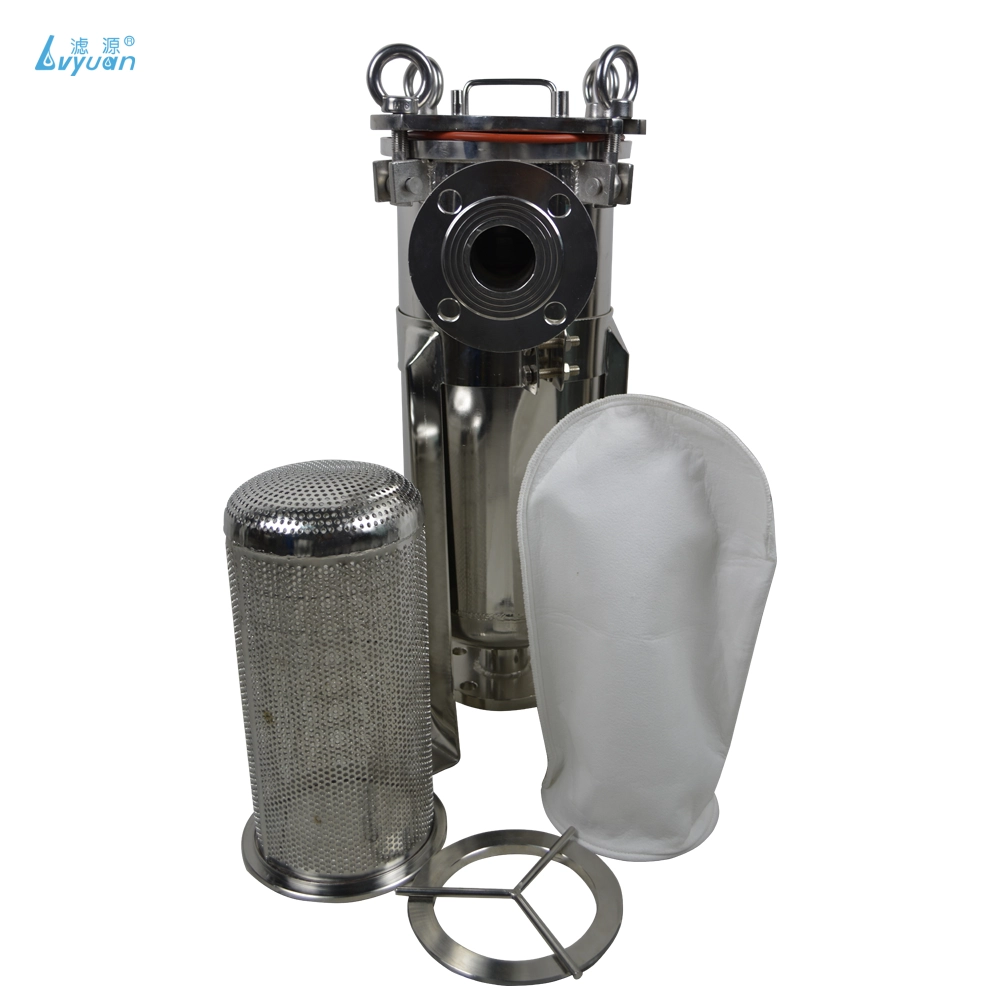
Bag filter housing
Bag filter housings are essential components in industrial filtration systems, designed to remove contaminants from liquids. To enhance the functionality and efficiency of bag filter housings, various features can be incorporated.
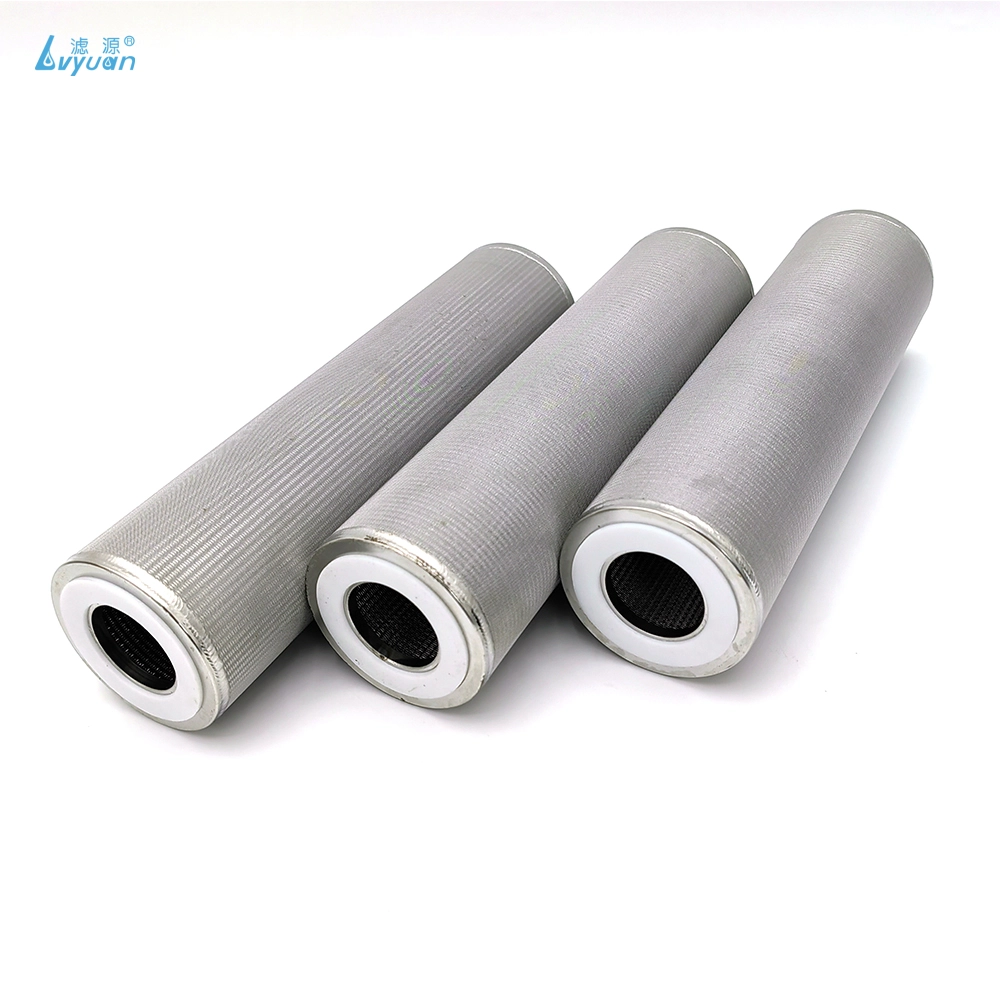
Sintered wire mesh filter
Benefit from outstanding high-pressure resistance and consistent filtration efficiency with Lvyuan's sintered metal mesh. Our sintered wire mesh finds versatile applications in diffuser screens, centrifuges, breather vents, fluidized beds, chromatography, polymer processing, petrochemical industries, hydraulic filters, and more.
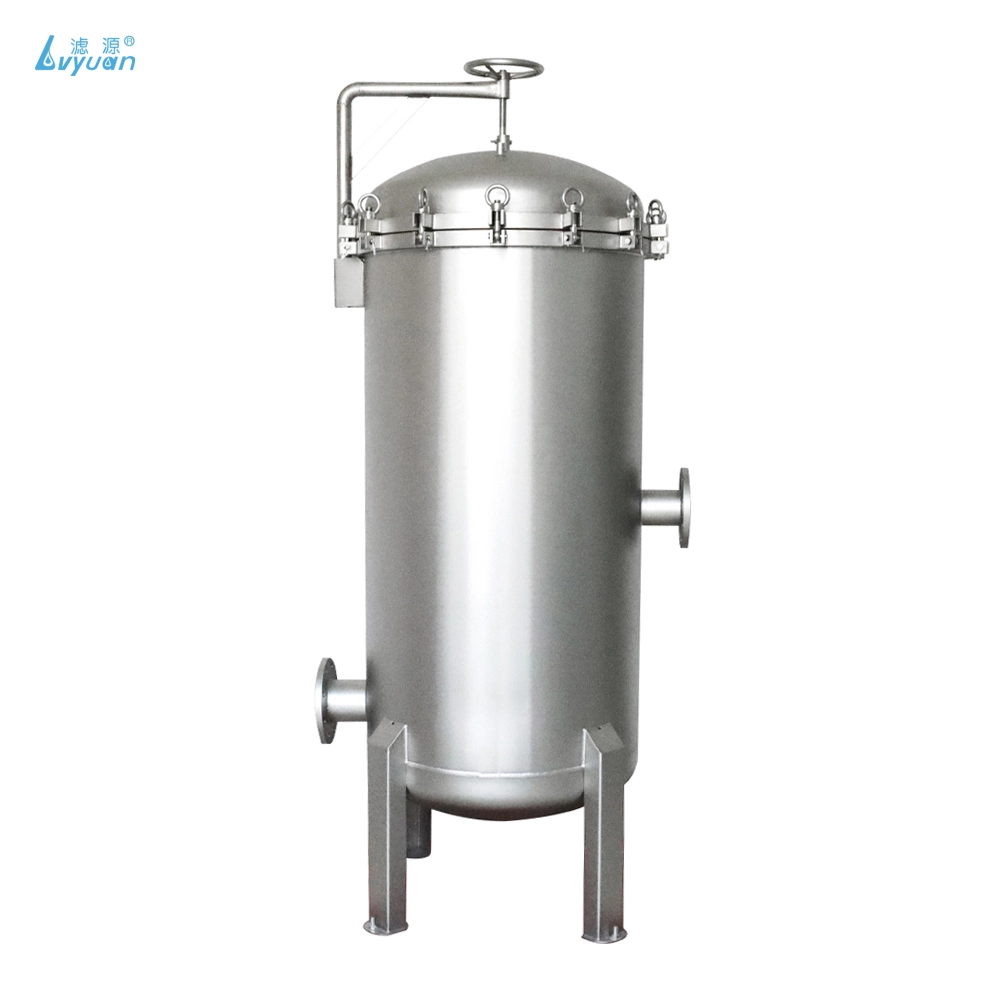
Stainless steel multi cartridge filter housing
Discover unparalleled filtration efficiency with our Stainless Steel Multi Cartridge Filter Housing – a testament to precision engineering and reliability.
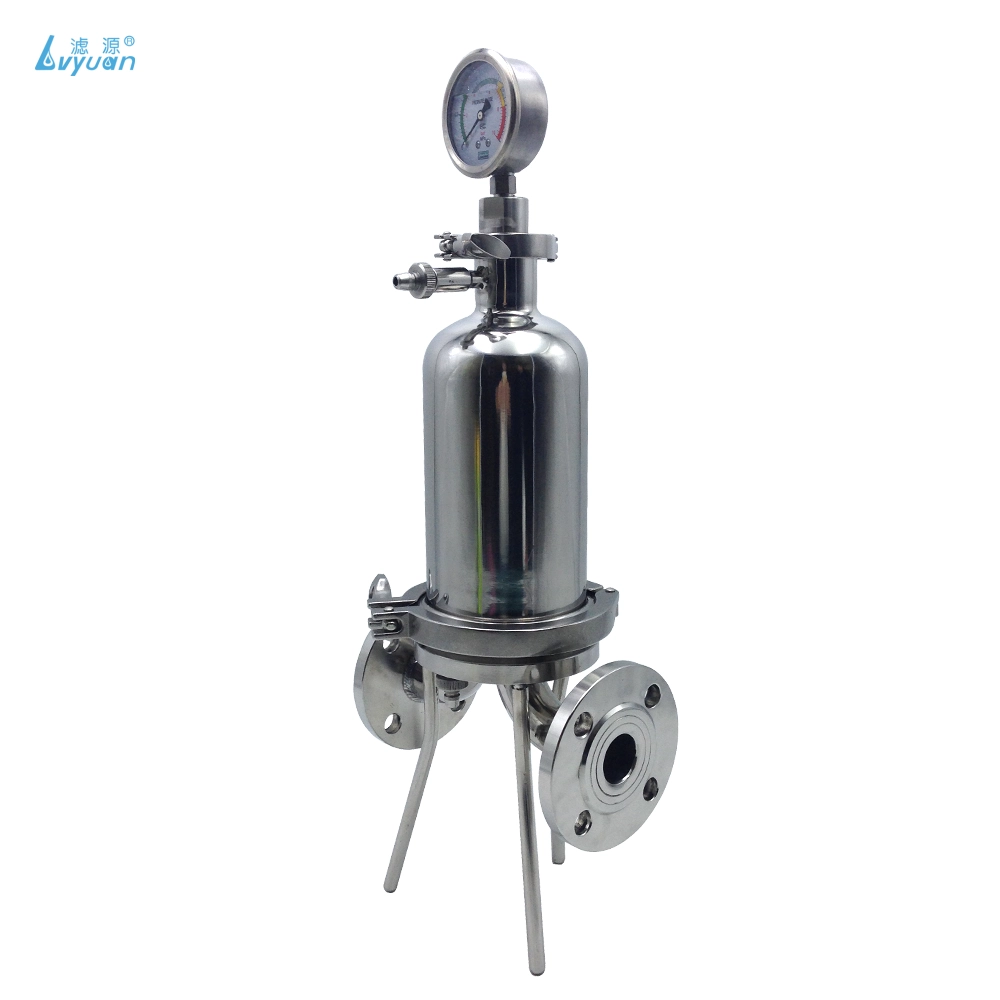
Sanitary filter housing
This filter housing will allow you to filter large volumes of nanoemulsion with ease. Sanitary vent and drain valves permit easy venting, draining, sampling, or integrity testing operations. The new cartridge locking design features additional cut-outs for traditional half-moon portions of the Code 7 bayonet locks, enhancing clean ability and drain ability.
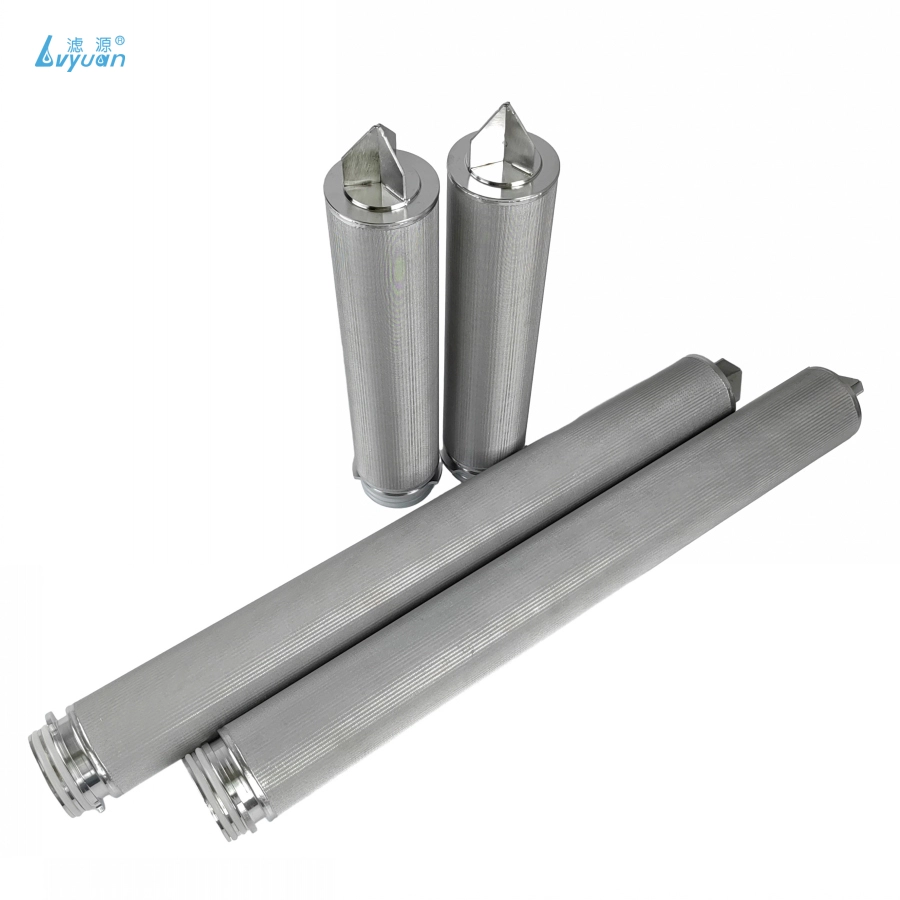
stainless steel filter water
Lvyuan’s sintered stainless steel filter stands as a pivotal filtration element crafted through a meticulous sintering process, with stainless steel serving as the core material.
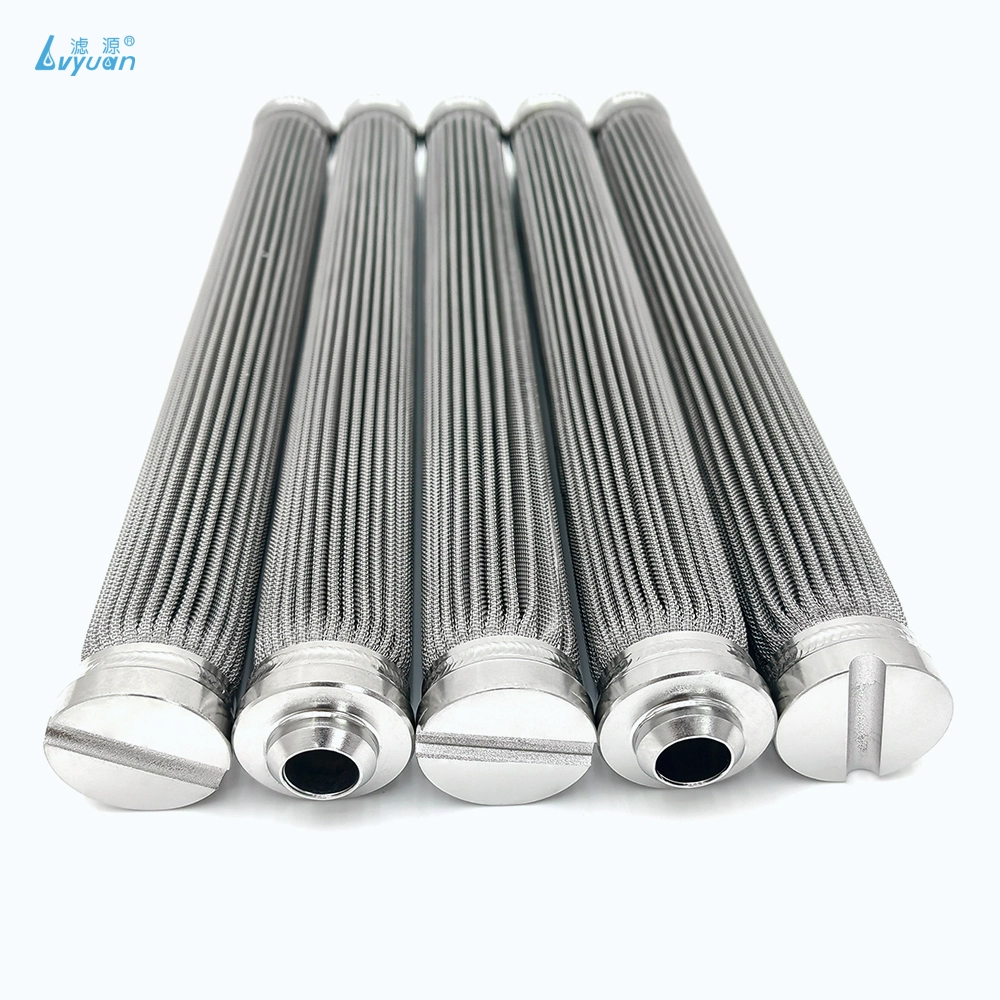
Stainless steel pleated filter cartridge
Lvyuan Stainless Steel Pleat Filter Cartridge constructed from high-quality SS 304 or SS 316L material, this filter exhibits exceptional resistance to high temperatures and rust.
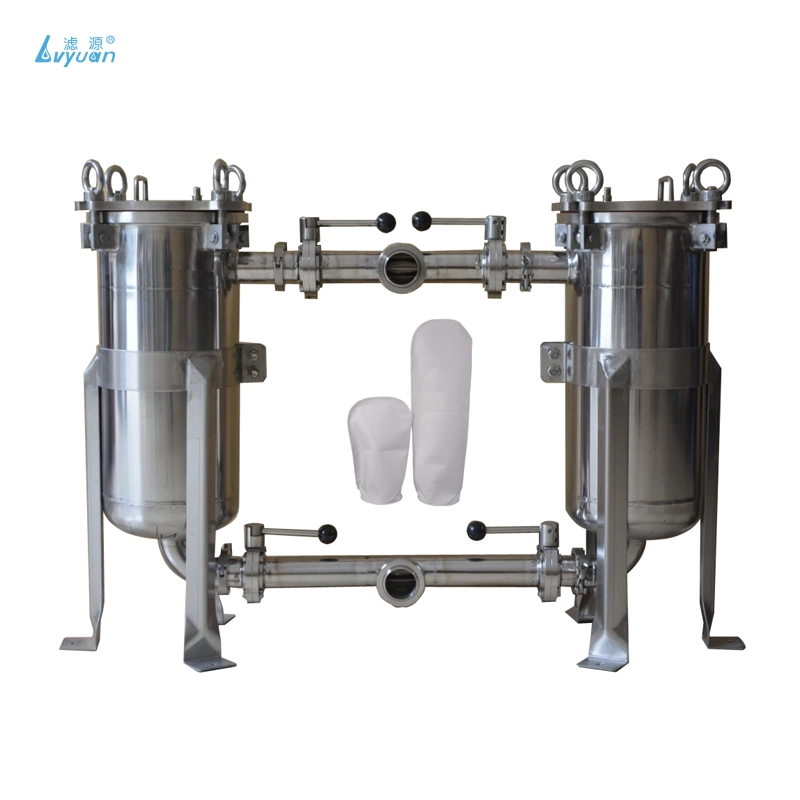
Stainless Steel Duplex filter housing
As the manufacturer, we offer a comprehensive range of Duplex Filter Housings designed to provide efficient and reliable filtration solutions for various industrial applications.
© 2024 Lvyuan All Rights Reserved. | Privacy policy • Terms and conditions